Technical Presentation 5 July 2023: HMAS Choules – Capability Assurance Programme
Lachlan Rowley, Engineering Manager, Atlantic & Peninsula Australia, gave a presentation on HMAS Choules SEA3030 Mid-Life Upgrade, to a joint meeting of the NSW Section and IMarEST ACT & NSW Branch in the Henry Carmichael Theatre, Sydney Mechanics School of Arts in the Sydney CBD, with IMarEST Committee Member, Steve Morant as MC, and streamed live on 5 July. The presentation was attended by 36 with an additional 17 online.
Introduction
HMAS Choules (ex RFA Largs Bay) is one of four Bay-class landing ships which the Australian Defence Force purchased from the Royal Fleet Auxiliary in the UK. She underwent a major refit to make her suitable for RAN service, arrived in Western Australia in December 2011, and was commissioned into the Royal Australian Navy as HMAS Choules on 13 December 2011.
Principal particulars of HMAS Choules are
Length 176.6 m
Beam 26.4 m
Draft 5.80 m
Displacement 16 190 t
Crew 158 officers and sailors
Capacity 356 troops (standard)/700 (overload)
32 Abrams tanks
150 light trucks
2 LCVP (landing craft, vehicle and personnel)
1 LCM8
2 mexeflotes (powered landing rafts)
2 helicopters
Main engines 2Wärtsilä 8L26 engines
each 2240 kW each
2Wärtsilä 12V26
each 3360 kW
Auxiliary 1Wärtsilä genset
Propulsion 2azimuthing thrusters
Manoeuvring Bow thruster
Speed 18 kn
Range 8000 n miles at 15 kn
Lachlan began his presentation with an overview of the SEA3030 Project, and the Refit Period 2021–22.
The major goal of the SEA3030 Project was a capability assurance programme—there were originally 44 discrete engineering changes but, over the course of the project, this was increased to 57. They included a HVAC upgrade (five new chillers, renewal of air-handling units and fan-coil units, new chilled-water pipework and flow philosophy), dry exhaust upgrades, ballast-water treatment facilities, galley upgrades, RHIB davit upgrades, new reverse-osmosis fresh water plants, new sewage treatment, stability upgrades, propulsion converter upgrades, diesel generator crankcase breather system upgrade, working air upgrades, fixed fire-fighting system upgrades, radar upgrades, and IPMS (Integrated Platform Management System) refresh. Also included were some capability additions to HMAS Choules: Close-in Weapons System (CIWS), Nixie decoy system, and Personnel and Magazine Ballistic Protection.
Some numbers from the Refit Period 2021–22 give an idea of the scope of the work done. This was the largest refit delivered on Garden Island in 15 years, with a budget of $180 million for the upgrade program, and $53 million for the maintenance work done in parallel: 1545 planned maintenance tasks, 476 corrective work orders, and $11 million in general support activities (scaffolding, painting, tank cleaning, etc.) There were 35 weeks of production, including 18 weeks in dry dock, and 17 weeks alongside. There were 675 000 man-hours of production, utilising 2500 individuals. The good news was that there were no major safety incidents, only 28 minor safety incidents and 8 man-hours lost due to injury.
Exhaust System Upgrade
The upgrade to the exhaust system was considered necessary for a number of reasons. Personnel safety was principal among them, as the exhaust stacks exiting the hull at the aft end of the flight deck above the transom created plumes across the decks during mooring. The installed wet exhausts inherit issues, with the water feed pipes being thick-walled mild steel and having corrosion problems after 12 years in service. The system was also prone to flooding the main engines by soot blocking drain pipes or valves incorrectly aligned. This occurred during ship build, and then again whilst in operation. Then there were the environmental optics with soot flowing into the sea on engine startup which wasn’t a good look in Sydney Harbour.
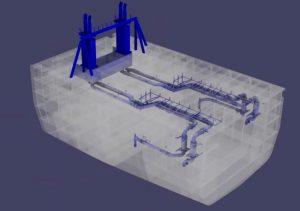
Exhaust design from engines to new exhaust stacks (midships) (Diagram courtesy A&P Australia)
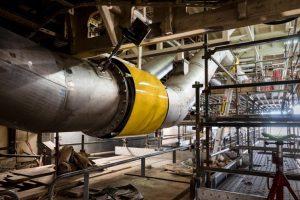
Exhaust in production standing on scaffold in vehicle deck (Photo courtesy A&P Australia)
The wet exhaust system leading aft and exiting the hull at the aft end of the flight deck above the transom was removed, and replaced with new dry exhaust stacks exiting vertically at midships. In the process there was much collaboration with Australian industry, and the solution provided safety and reliability with decreased maintenance costs, and the bonus of making additional compartments available for new machinery and storage spaces.
HVAC Upgrades
Upgrades to the heating, ventilation and air-conditioning systems were considered necessary as they had been designed for UK conditions, and were seriously under capacity for Australian conditions. The system had limited redundancy built in and the ageing chillers were becoming less reliable and more expensive to maintain.
This upgrade was the largest change during the refit, with the removal of the old individually-looped chillers (2´1350 kW main chillers, and 2´450 kW and 2´70 kW chillers) and installation of new chillers on a constant-flow circuit (5´1000 kW chillers and a DG fresh-water cooling modification). The upgrade increased the overall cooling capacity by 35%.
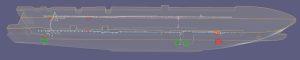
Chillers on HMAS Choules (old chillers in red, new chillers in green) (Diagram courtesy A&P Australia)
This change affected approximately 60 compartments across the ship.
During set-to-work, the chilled water system was filled which led to a very strong “team bonding session”, as the team was stationed around the ship with radios to identify and rectify inevitable leaks.
The supply chain in Europe was also severely hampered by the pandemic which led to late delivery of components, and the new chillers required to be flown to Australia to meet the schedule. The HVAC upgrades were a massive undertaking, required the use of many different installation partners, and boasted a huge AIC (Australian Industry Content) with the system being wholly designed and installed using Australian engineers and labour force.
Ballast Water Treatment System
The Ballast Water Treatment System (BWTS) required an upgrade to bring the ship into line with IMO’s 2017 requirements for treating ballast water.
This required major rework in Auxiliary Machinery Room No. 1 for the forward ballasting system (two ballast pumps and one new modular BWTS), and in the Ballast Pump Room for the after system (four ballast pumps and one new modular BWTS).
The inherit tight confines of these spaces presented a challenge to fit the new equipment in these locations, along with other engineering changes in concurrence. These challenges were overcome with the use of the “PureBallast” modular system, 3D scanning and modelling of the compartments, pre-assembly in the workshop and then final installation on the ship.
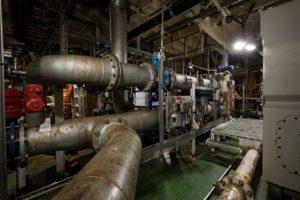
Forward ballast water treatment system installation (Photo courtesy A&P Australia)
Removal and Insertion Routes
The removal and insertion of items of equipment required six major inserts in the hull of HMAS Choules, each spanning approximately 3 m´5 m. Locations included:
- Auxiliary Machinery Room No. 1 (Fwd) — Support for the BWTS, sewage treatment plants (´2) and a chiller
- Auxiliary Machinery Room No. 2 (Midships) — Support for chillers (´2), reverse-osmosis plant (´2) and water-mist equipment
- Technical Equipment Rooms (Port and Starboard) — Out with old chiller, in with new
- Propulsion Converter Rooms (Port and Starboard) — Out with old converters, in with new
- Many more smaller inserts (in bottom side tanks, and for the topside exhaust) were required
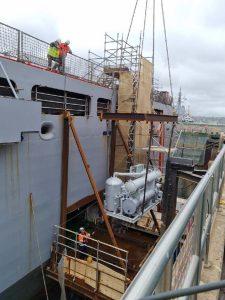
Hanging platform welded to ship’s side for aft chiller installation (Photo courtesy A&P Australia)
To support these major removals and inserts, a set of jigs, platforms and fixtures were also required. Three of the original platforms, originally fabricated for the FFG upgrade programme were modified and repurposed for the work on HMAS Choules. The fourth “hanging” platform was purpose designed, built, and load tested for use on the port technical equipment compartment.
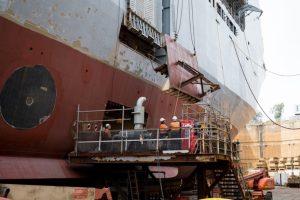
FFG platform in use on HMAS Choules (Photo courtesy A&P Australia)
Underwater Hull Coating
It had been noted that the hull was extremely fouled at previous dockings and on the current docking, so a change in coating was considered late in the programme. Hempel X7 was applied to the hull, a silicone-based coating with integral biocide designed to minimise hull growth drag through water.
This has led to considerable fuel savings and propeller RPM at high lever settings. Recent diving inspections, 15 months after leaving dock, showed minimal growth on the hull.
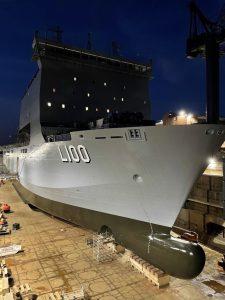
HMAS Choules with new antifouling applied (Photo courtesy A&P Australia)
Challenges
There were a number of challenges during the Refit Period 2021–22, many due to the sheer volume of work undertaken:
- there were workforce shortages due to the pandemic;
- permits for hot work—an average of 45 per day—needed additional ship’s staff and safety staff;
- cranage was in short supply—they had four cranes at times to support more than 12 000 lifts through the period;
- work in confined spaces required rescue teams to be on standby;
- deconfliction between contractors working in the same compartments;
- lost time due to the pandemic totalled ~20,000 man-hours;
- there were rain delays as it was the wettest year in history); and
- there were supply-chain issues with the pandemic and European unrest.
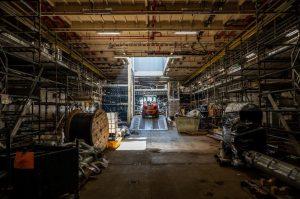
Vehicle deck looking aft showing volume of work and scaffolding (Photo courtesy A&P Australia)
Results
With the changes made to the propulsion converters, the streamlined underwater hull coating, the upgrades to cooling and general in-service pod maintenance, for the first time in the past six years the ship has been able to maintain maximum power output through the pods!
In addition, the ship’s sea trials went through the whole programme without major issue and successful set-to-work of all systems, a huge achievement for many systems to be upgraded and successfully set to work without a defect rectification period.
As a matter of interest, the UK MoD is having some similar problems with their remaining three Bay-class LHDs, especially with the HVAC system, and have not been able to solve them, so they are now particularly interested in the upgrades which Australia has made.
“Delivering Success Together”—Atlantic and Peninsular Australia’s ethos was reflected in the presentation as credits were notes for the wide array of design and installation partners who helped deliver a successful refit.
Conclusion
Atlantic and Peninsula Australia and their design and installation partners have completed a successful refit and upgrade to HMAS Choules, despite significant challenges along the way. A&P continues to deliver HMAS Choules in-service maintenance and engineering support, and look to continue naval engineering support.
HMAS Choules continues to be ready and available to the Royal Australian Navy for amphibious operations.
Questions
Question time was lengthy and elicited some further interesting points.
The presentation was recorded and is expected to be available soon on the RINA YouTube channel.
The vote of thanks was proposed, and the “thank you” bottle of wine presented, by Greg Hellessey. The vote was carried with acclamation.
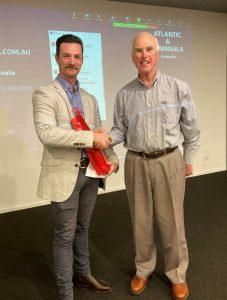
Lachlan Rowley (L) and Greg Hellessey (Photo Phil Helmore)