Hull stress monitoring has been a feature of commercial shipping since the 1990s, but according to Terje Sannerud from marine structural monitoring specialist Light Structures, it is today finding applications for improving ship design, insightful maintenance and potentially extending the period between dry-dockings allowing for cost savings without compromising ship safety.
Ships can become damaged, disabled and even destroyed by a variety of events – collisions, groundings, fires and explosions are all examples that are sudden and unexpected events. However, many more ships are affected by stresses on the structure that develop over time as with fatigue or be caused by factors such as poor stowage of cargo or weather and waves.
A ship’s hull is not intended to be a rigid structure but must be designed to be able to meet all the hydrostatic and hydrodynamic loadings and forces that are likely to be imposed on it during the normal course of trade within its intended areas of operation.
Hydrodynamic forces are encountered when the ship is in motion and will typically involve the effect of waves causing pitching, rolling and slamming. These forces will affect any vessel type to some degree and require the vessel to be flexible. Hydrostatic forces are those that can be identified in calm water and are imposed by the location of the ship’s machinery and cargo. Hogging and sagging are typical examples and will particularly affect bulk carriers.
Design development and safety considerations
Modern ship design tools such as CFD and FEA are intended to overcome the issues around stress and fatigue, but they are not perfect. Incidents such as the losses of the five year old 8,100teu container vessel MOL Comfort in 2013 and the VLOC Stellar Daisy in 2017 were both attributed to critical structural failure. MOL Comfort’s series of sister vessels were subsequently strengthened to avoid a similar fate and while the Stellar Daisy was a much older vessel, having been built in 1993 as a VLCC and subsequently converted in 2008 when strengthening work on the deck and tanktops was done, her demise resulted in many other similarly converted vessels being withdrawn from service.
Rapid developments in ship size and specialisation along with new materials pose problems for ship designers in taking into account the stresses likely to be encountered. This was especially true of bulk carriers built in the last two decades of the 20th century several of were lost in tragic circumstances. Consequently in 1994 the IMO issued MSC/Circ.646 which recommended the installation of hull-stress-monitoring systems to facilitate the safe operation of ships.
Such systems should provide real-time information on the motions and global stresses on the ship’s hull while navigating and during cargo operations. They should sound alarms when pre-determined stress levels are exceeded allowing the crew to take appropriate action which would normally be to reduce speed if slamming is occurring, possible transferring loads such as ballast or fuel to reduce other hydrodynamic forces.
Seeing the light on stress monitoring sensors
A typical hull stress monitoring system would employ a number of strain gauges – these are generally electro-mechanical or fibre optics based. Light Structures’ SENSFIB solutions come into the latter category and make use of Fibre Bragg Grating (FBG) technology which offers several advantages.
Electro-mechanical gauges are usually mounted on deck and therefore require protection. The protective boxes can be quite large and create obstructions, they are also subject to forces that may cause damage to the system. Because of the small, light form factor of fibre optic FBG sensors, they can essentially be located below deck. As long as they are positioned in the best place to provide the best readings on the specific measured force – a task carried out by Light Structures’ experts or trained third party engineers – it makes no difference if they are inside or out.
Light Structures’ FBG sensors are protected by a thin layer of non-woven fibre glass. This material was selected because woven fibre glass can actually strengthen the hull, so the measurements would not reflect the actual vessel’s design. Initially sensors were left ‘bare’, but it was found that painting them with the same paint used on the surface can prevent very rare cases of corrosion on the metal below the sensor, which could affect the reading. When painted over SENSFIB sensors simply become part of the structure.
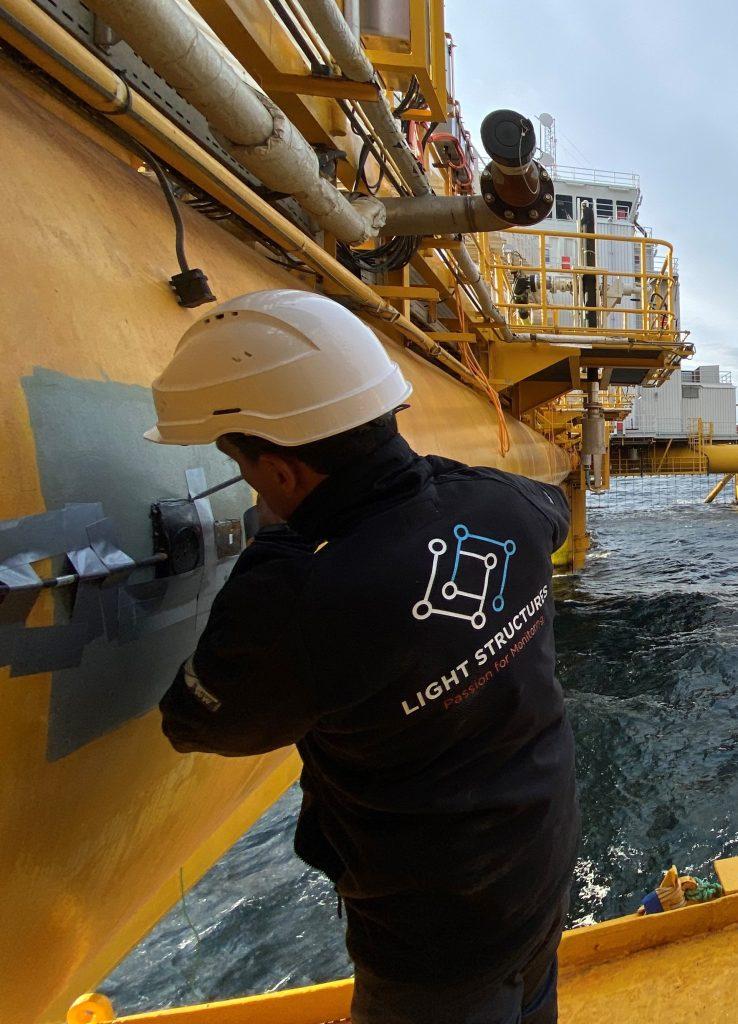
Sensor installation on the Ocean Farm 1 offshore aquaculture facility
Making use of data
Data from hull stress monitoring systems should whenever possible be captured by the Voyage Data Recorder for use in any investigations that may be necessary after an incident, but through reports or transferring data to cloud platforms, data can also be employed to verify and improve ship designs thus making it a valuable resource for ship designers during service and when considering new vessels of the same or similar design.
In the first instance, SENSFIB data is used to support decision making by the master and bridge crew in real-time onboard. However, as it also stores historic data, custom made reports can be produced for owners and operators. These reports can be used to compare performance with design predictions allowing for improved designs and for owners to make informed decisions about future use and operation of the ship.
Reports from any hull monitoring systems can be produced by classification societies but Light Structures’ strategy is to produce the reports inhouse using its own experts in order to reduce costs for the ship owner. The company conducts a lot of event analysis and looks at the data from extreme loading, where sensor measurements can be compared to the alarm limits and explored in greater detail.
The reports also look at stress induced fatigue, which is an important measurement to validate a vessel’s design life. When looking at total fatigue it may reveal that the vessel actually has a much longer design life than initially expected, which could be very important data for the owner affecting such things as planned disposal or transfer to other trades.
The reports can be used to calculate the fatigue cause per trade area or for a specific storm. For instance, high loads from whipping in a storm can contribute to a significant amount of the fatigue accrued during a single voyage, which could be useful for naval architects to consider based on the type of vessel and routes it will take. The fatigue profile is useful as it can show the vessel’s predicted life according to its current trading profile, giving insight into the vessel’s application and potential to change it.
SMART structural health monitoring offers many benefits
Increasing digitalisation in the maritime industry has resulted in the development of Smart Ships by many shipyards and classification societies adopting Smart Ship notations and rules for their use. Smart designations may refer to many attributes including navigation, machinery health and cyber security as well as structural monitoring.
Classification societies are at the forefront of maritime digitalisation not least because they recognise that the quality of data that is now becoming available for many systems onboard ships is such that it is often equivalent to, or better than, that obtained by physical examination. This is confirmed by the fact that many class societies are now offering virtual surveys under certain circumstances. This was happening before the Covid pandemic but accelerated during and since.
Making the case for EDD
Most ships are required to be dry-docked twice every five years with an interval not exceeding 36 months between dockings. The reason for this lies in SOLAS which requires a ship’s bottom to be inspected twice in each 5-year period. However, extended dry-docking (EDD) intervals for certain types of new vessels became acceptable more than a decade ago initially for new ships – later extended to ships up to ten years of age – and through to their reaching 15 years. The concept was promoted by classification societies which interpreted the SOLAS requirement for an inspection as being made possible using an in-water survey rather than a drydocking.
Class societies were not the sole arbiters however because flag state rules often required the inspection to take place out of water. That said, most flag states were happy to adopt the concept which allowed a single dry docking every 7.5 years although there were numerous ship types- passenger vessels, bulk carriers and tankers not permitted to take part in such programmes. One requirement that many class societies made was that the anti-fouling coating should be capable of functioning between the extended dry docking periods.
As hull stress monitoring is starting to be more considered by class, under smart notations, it makes sense to give added credence to ships employing it in the context of EDD. There has been a positive step in this direction as BV has agreed that SENSFIB data can be used to argue the case of extending a dry-docking interval on a vessel-by-vessel basis. It is the shipowner that must have the conversation with the classification society, but the Light Sturctures data and reports are essential for this to happen.
Drydocking costs obviously vary depending on ship types, age and size but with costs of several hundred thousand dollars or more for a larger ship type and around 20 – 30 days loss of revenue and perhaps chartering in a replacement on a liner service, the costs are always significant. Therefore, the opportunity to reduce that becomes very attractive.
Linking the data from a SENSFIB system with a digital twin could also allow for any required hull repairs to be assessed in advance and required steel work to be prefabricated before any dry docking or afloat repairs are undertaken. Furthermore, as with any condition-based maintenance system prior notice of impending issues allows for better planning for vessel employment.