Wind Propulsion Conference 2023
In Association with:
The current use of alternative fuels and renewable energy sources within the shipping industry is still relatively scarce. Growing environmental legislation and concerns are driving the need to develop and apply innovative alternative power and propulsion technology for ships.
Now, industry players are increasingly putting a modern spin on one of the oldest concepts in shipping: harnessing the power of wind for ship propulsion.
Since the inaugural conference in 2019, the annual event has attracted a high level of interest in the maritime community. Attending speakers and delegates span the technology companies, academia, ship owners and industry associations. The 2023 conference agenda promises to bring those attending fully up to speed with recent technological, design and policy developments, and cast the minds of attendees into the future landscape for wind propulsion technology.
Sponsored by:
Speakers
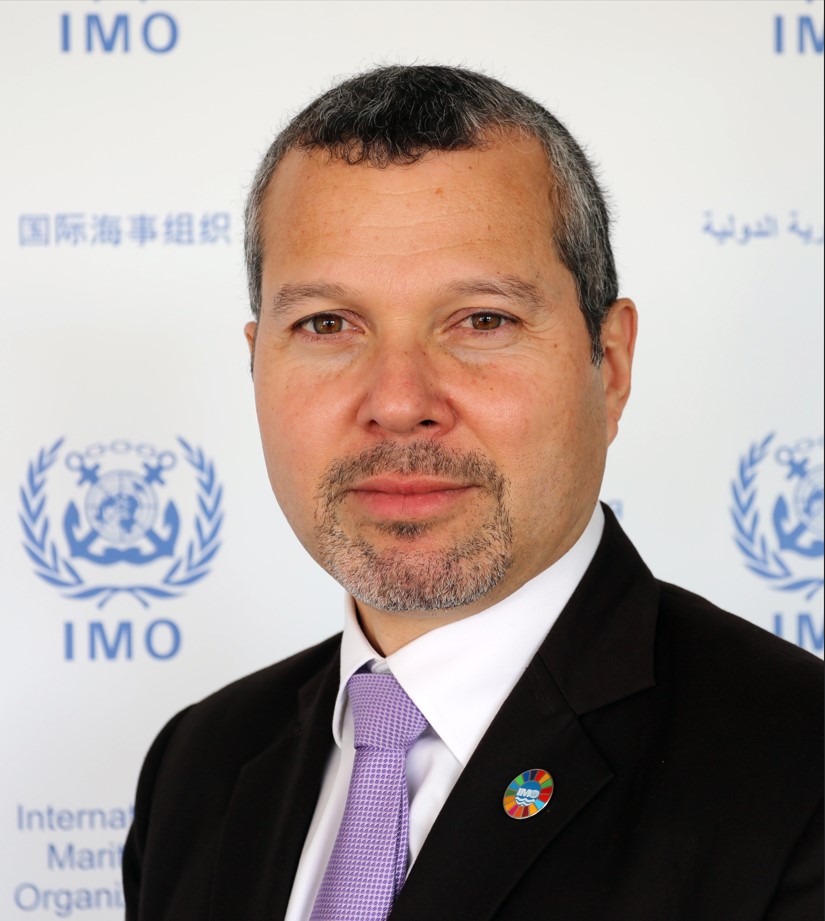
Arsenio Dominguez, Director, Marine Environment Division, International Maritime Organization
Mr. Dominguez currently serves as Director, Marine Environment Division of the International Maritime Organization (IMO), having served previously as Director, Administrative Division and Chief of Staff. Before joining IMO in July 2017, Mr. Dominguez worked for the Panama Maritime Authority starting in 1998 as Head of the Regional Technical and Documentation Office for Europe and North Africa, and as Alternate Representative and Technical Adviser of Panama to IMO from 2004 to 2014. In July 2014 he was appointed Ambassador and Permanent Representative of Panama to IMO.
From 1998 to 2017, Mr Dominguez represented Panama at IMO, as well as at the International Labour Organisation (ILO), the International Oil Pollution Compensation Funds (IOPC Funds) and the International Mobile Satellite Organisation (IMSO). He also represented Panama at several shipping conferences, forums, exhibitions, seminars and workshops.
Having chaired a number of meetings at international organisations, Mr. Dominguez was elected Chair of IMO’s Marine Environment Protection Committee (MEPC) from 2014 to 2017, having previously served as Vice-chair from 2012 to 2013. He was also elected Chair of the Technical Committee at the 29th IMO Assembly in 2015, Chair of IMO’s Maritime Safety Committee (MSC) Working Group on Maritime Security and Piracy from 2010 to 2014, and Vice-Chair of the Subcommittee of Dangerous Goods, Solid Cargoes and Containers (DSC) from 2009 to 2011.
Mr. Dominguez holds a Naval Architect degree from Veracruzana University, Mexico; an MBA in Management from the University of Hull, and a Certificate of Higher Education in International Law and European Politics from Birkbeck University, both in London, England.
Topics
- Market level assessment
- Concept level assessment
- Technology level assessment
Abstracts
Wind Propulsion and Underwater Noises Mitigation
Pierre Cordier, XP SEA
From various scientific studies, we know that vessels Underwater Radiated Noise (URN) has a significant negative impact on marine life. The shipping industry and the maritime regulations are therefore expected to mitigate these noises in the coming years. For some players, the work has already started.
URN emitted by vessels mainly come from propeller and hull appendages, in particular when cavitation occurs, and machinery equipment.
Studies measuring in-situ vessels’ URN show a clear correlation between ship speed and URN with large differences between types of vessels and speeds. However, modern ship designs allow for low URN by different means while the average speed is kept reasonable.
Ship speed and propeller rpm reduction are the most efficient measures to reduce URN and is an opportunity to increase the contribution of wind propulsion which is the most silent means of propulsion.
Indeed, depending on the technology and the environmental conditions, wind propulsion may represent 100% of the power contribution up to a certain ship speed limit. Above that speed, its contribution decreases while the conventional propulsion contribution increases exponentially.
Among the parameters, the thrust given by the wind decreases drastically with ship speed as the Apparent Wind Angle moves towards head wind. Reducing the ship speed from conventional propulsion increases the wind thrust, and more so, its relative contribution to propulsion.
The question is therefore “What would be the maximum speed achievable combining wind and conventional propulsion at which the URN would be acceptable for the sea life?”
Performance Prediction of Wind Propulsion Technologies via CFD
Rodrigo Azcueta, Cape Horn Engineering
Global efforts to reduce the environmental impact of the shipping industry have accelerated rapidly in recent years, with new measures by IMO, such as the EEXI for existing ships and EEDI for new designs, set to come into force in January 2023. From 2022 the IMO accepts CFD as a mean to provide the vessel reference speed needed in the EEXI/EEDI calculation.
The adoption of Wind Assisted Ship Propulsion devices (WASP), such as wing sails, suction sails, Fletner rotors or kites is gathering momentum as an easy way of improving fleet performance. However, in order for the shipping industry to fully embrace these new technologies, accurate CFD analysis of potential savings and risks is required. It is important that this assessment be carried out by independent, technology agnostic, CFD organisations.
This paper presents a wide range of CFD analyses, including verification and validation studies, which aims to demonstrate the potential of CFD to support in the adoption of these novel technologies. The case studies presented are based on the SINTEF Ocean bulk carrier benchmark for which good quality model testing results are available. Open water propeller simulations, resistance tests at model and full scale, propulsion tests with actuator disk and with rotating propeller and 6 DOF simulations for motor-sailing conditions are presented. The importance of accurate CFD practices for EEXI/EEDI calculations, in particular when introducing ESDs and WASP devices are highlighted. The requirements of demonstrating the qualification of the CFD solution by performing numerical uncertainty analysis following the ITTC and IACS recommendations is described.
Synergies of wind-propulsion and Gate-Rudder technology
Norbert Bulten, Wärtsilä
In order to reach the challenging EEDI targets significant steps in application of energy saving technologies need to be made. Given the variety of the different concepts, it is important to identify which combinations give additional synergies. Both wind-propulsion and Gate-Rudder technologies have a proven track record of significant energy saving in operation. The effective wind-assisted propulsion is found for sails, rotor-sails and suction-sails. Gate-Rudder technology has shown clear fuel saving on numerous vessels as well.
Wind-assist is known to come with additional sway forces, due to the varying direction of the wind-speed. This increases the demands on the vessel course-keeping capability. With effective wind-assisted propulsion the loads on the conventional propeller are supposed to be reduced, which come with reduced effectiveness of the rudder, downstream of the propeller. The main driving factor of the Gate-Rudder system is not the propeller wash, though the vessel speed, which is maintained with successful wind-assisted propulsion. As a consequence, the course-keeping capability is maintained, which gives a clear synergy of the combination of wind-assisted propulsion with Gate-Rudder technology. In the EU-project CHEK these aspects are investigated based on full scale CFD simulations. The paper will present the numerical methodology which has been developed to determine the vessel maneuvering capability in an effective way. Decoupling the aerodynamics and the hydrodynamics allows for a generic approach of different wind-assisted concepts.
Preliminary Study on the Propeller and Engine Performance Variation of Commercial Ships with Wind Propulsion Systems
Martina Reche-Vilanova, North Windship Technologies
Wind Propulsion Systems (WPS) for commercial ships are vital to achieving the IMO targets on energy efficiency and GHG emissions. Most WPS will operate in a hybrid mode alongside actual main propulsion units. This will affect the propeller and engine operating conditions and thus, their performance. The present paper discusses a preliminary assessment of commercial ship propeller and engine performance variation as a function of the wind power installed for two propeller plant types (Fixed Pitch Propeller, FPP, and Controllable Pitch Propeller, CPP) and two operational modes (constant speed and constant RPMs). The proposed contribution is based on empirical and analytical methods requiring minimal input data. It aims to provide general trends and contribute basic knowledge on this matter. A cost model is included for a cost-benefit assessment of both propeller types. This leads to advice on which systems to install as a function of WPS installation size. The results show that the additional wind propulsion unloads the propeller, which results in a beneficial increase in propulsive efficiency and a detrimental rise in the main engine specific fuel oil consumption (SFOC). However, both effects result in overall favourable propeller and engine performance variation. The FPP appears to be more suitable for wind-assisted installations (wind provides auxiliary propulsion, <50%), whereas the CPP seems to be for wind-powered installations (wind is the main propulsion, >50%).
Key Performance Indicators for Wind-Powered Ships
Sofia Werner, RISE
The wind propulsion industry evolves rapidly, and many new technologies emerge on the market. This calls for standardised ways to express the performance of wind propulsion technologies (WPT) in a transparent manner. The wind propulsion community has, however, not yet agreed on common key performance indicators (KPI). This complicates comparing technologies, puts the level playing field at risk, and delays investment decisions. In this paper we discuss a number of different KPIs describing the ability of a WPT to generate thrust and save fuel. Suggested KPI definitions have been gathered through a series of industry workshops in co-operation with the International Wind Ship Association (IWSA), International Towing Tank Conference (ITTC) and the EU Interreg project WASP. After an explanation of the underlying assumptions and calculation methods the suggested KPIs are exemplified for several generic ships equipped with wind propulsion systems typical for their size. Results are discussed in the light of
- Facilitating a fair comparison between technologies
- Being descriptive and easy to understand
- Resonating with shipowners and operators
It is hoped that these case studies will spark further discussions withing the industry and facilitate finding useful and standardised metrics to assess wind propulsion technologies.
PERFO: Methodology benchmark for Wind Assisted Propulsion Ship Performance Estimation
Juliette Bataille, Bureau Veritas Solutions M&O
Recently, the maritime sector has seen a significant development of Wind Propulsion Assistance Systems (WASP) to act towards reducing the global emissions induced by goods transportation at sea.
The installation of a WASP onboard a vessel decreases the propeller required thrust but introduces significant side forces, modifying the attitude of the vessel and adding drift-induced resistance. Hence, it is unsuitable to account for the gains as a simple reduction of effective power.
PERFO is a collaborative project between the French Oceanographic centre Ifremer, the naval architecture firm Stirling Design International and the engineering office Bureau Veritas Solutions M&O.
The project consists in developing a methodology to estimate a vessel’s performance with a WASP onboard. Its robustness is insured through CFD simulations-based validation process, an extensive literature review and close cooperation with WASP suppliers. The project aims at providing ship owners with ship performance predictions validated on study cases.
Within PERFO, a wind-assisted ship power prediction tool has been developed. It balances the hull’s hydrodynamic response to the transverse force generated by the WASP, inducing a couple of drift and rudder angles. The interaction between the superstructure of the vessels and the WASP is also accounted for.
Successive levels of modelling are proposed; each tailored to the project stage and needs, to optimise engineering time and computational cost. As a first level, empirical methodologies are used. Later RANSE CFD.
The open-source benchmark vessel ONRT has been used as a study case. Then, vessels from the Ifremer’s fleet are studied.
WISP2 PROJECT ON WIND PROPULSION PERFORMANCE PREDICTION METHODS AND MANOEUVRING
Rogier Eggers and Anton Kisjes, MARIN
The number of ships equipped with wind propulsion, and the number of credible suppliers of wind propulsion systems are rapidly increasing. It appears that the shipping industry is increasingly seeing the need for design changes in view of the climate crisis and simply due to more strict regulations on greenhouse gas emission performance of ships. The uncertainty in investment has decreased as various projects in the last years provided evidence on the realised savings.
Nevertheless, there is much work still to be done to bring wind propulsion to its full potential. In 2019 MARIN and ABS started the WiSP JIP (Wind Ship Propulsion Joint Industry Project), followed up by WiSP2 which is to be concluded in 2023. The first WiSP project started on the premise that the increased uptake of wind propulsion was hindered by a lack of verified performance data as well as a lack of appropriate standards, rules and regulations. This was one of the main “barriers” as identified by the report by Nelissen et al[1] for the European Committee. At the conclusion of the first WiSP project, there was already an increase in reports from ships actually sailing with wind propulsion. The project itself contributed to the improvement of the EEDI & EEXI guidelines for wind propulsion[2]. However, knowledge and standards on prediction methods, certainly on more substantial contributions of wind propulsion, as well as better rules and regulations still appear to be needed.
The present paper discusses the performance prediction methods as explored in a follow-up, WiSP2. However, we will extend beyond “just” the steady condition, to manoeuvring & seakeeping. Compliance to the manoeuvring standards[3] is not trivial for many ships. In many cases, their course keeping ability is also an indication of the possibility to handle large side forces and yawing moments that are inevitable with wind propulsion. In this paper we will discuss replication of earlier seakeeping and manoeuvring tests in the WindLab project[4], as well as a more broad exploration of wind conditions with the MARIN Ferry[5] used as case vessel equipped with 4 Flettner rotors. The results of this work are used to show some scenarios of how the IMO manoeuvring standards may be interpreted. The results directly show, for two ship design cases, in which conditions it may be a challenge to comply, and where not. Also, other ship behaviour such as the maximum heel angle during a turn is evaluated, as in certain wind conditions these heel angles increase significantly.
[1] Nelissen, Dagmar, Michael Traut, Jonathan Koehler, Wengang Mao, Jasper Faber, and Saliha Ahdour. 2017. “Study on the Analysis of Market Potentials and Market Barriers for Wind Propulsion Technologies for Ships.” Delft: CE Delft.
[2] International Maritime Organization. 2021. “2021 Guidance on Treatment of Innovative Energy Efficiency Technologies for Calculation and Verification of the Attained EEDI and EEXI.” MEPC.1/Circ.896
[3] International Maritime Organization. 2002. “Standards for Ship Manoeuvrability.” Resolution MSC 137(76)
[4] Eggers, R., and A.S. Kisjes. 2019. “Seakeeping and Manoeuvring for Wind Assisted Ships.” In International Conference on Wind Propulsion. London, United Kingdom: Royal Institution of Naval Architects
[5] Ferrari, V, H vd Boom, AS Kisjes, and FHHA Quadvlieg. 2020. “Heel Angles in Turn and Passenger Safety.” In Sustainable and Safe Passenger Ships. Athens, Greece.
Novel Platforms for Optimising Renewable Energy Powered Ships
Ken Goh, Knud E. Hansen Australia
This paper presents the concept of a 50,000 DWT bulk carrier that uses wind and solar propulsion as the main source of propulsion. The concept uses a proa form with main hull and outrigger. The unique form allows the vessel to harvest wind and solar energy in similar quantities. This enables the proa to have more navigation options than a traditional sailing vessel that is inefficient in headwind conditions. Due to the unconventional form, much of the design has to follow first-principles engineering methods. The paper explores some of the main technical challenges and economics factors of the proa design and shows the potential of this concept.
WASP assessment from a Ship Designer point of view
Roberto Prever, NAOS Ship and Boat Design srl
Today, most of the WASP maker are concentrated on emphasizing the pure aerodynamic performances, translating that directly into fuel saving. If this could be accepted as the first approach, it is not saying the truth when a specific vessel shall be assessed.
Stability rules, operational-wise acceptable permanent heeling angle, new displacement due to device weight and ballasting requirements, are factors equally important for a holistic and practical assessment of the WASP.
The paper will explore practical aspects which should be considered to compare different systems, in relation with specificities of ships, and show how ranking the different WASP systems from that perspective, may lead to different considerations on the appropriateness of an installation.
Furthermore, ship manning is by far different from sailing yacht conducting. Crew has and will have limited training to properly conduct a sailing ship, and will regards WASP mostly as a simple device to reduce loads on the propeller, without caring too much of it. The consequences of such consideration on how a WASP system should be efficiently design shall be drawn.
Validation of Performance Prediction Program against Cyber-Physical Model Tests
Kristoffer Eide, SINTEF Ocean
The present paper describes a validation of a power prediction program (PPP) against physical model tests. The PPP software solves the motion of the vessel in 3DOF (surge, sway and yaw), where the applied manoeuvring coefficients, resistance curve and propeller characteristics comes from model tests. The wind propulsor model is based on CFD simulations (De Marco, et al. 2016). The SINTEF Ocean bulk carrier (SOBC-1) was chosen in the validation study due to recently performed cyber– physical empirical model tests (Sauder and Alterskjær, 2022), where the effect of the wind propulsors were included using a novel hybrid testing technique. In the experiments, the SOBC-1 model was running at self-propulsion, where propulsion was delivered from four numerically modelled Flettner rotors, in addition to a single screw conventional propeller. The force acting on the wind propulsors was applied on the model using a system of wires, connecting the model to actuators, that provides forces according to prescribed apparent wind conditions. In the present validation, the computed leeway and rudder angles, can directly be compared against the model test results. While the side force induced added resistance of the vessel is indirectly compared by evaluating the propulsion point of the single screw propeller and compared against measured RPM, torque and power during model tests. The validation is conducted for a set of apparent wind directions ranging from 30 to 150 degrees, while apparent wind speed varies from 10 to 20m/s.
References:
Thomas Sauder, Sverre Anders Alterskjær (2022) Hydrodynamic testing of wind-assisted cargo ships using a cyber–physical method. Journal of Ocean Engineering, Volume 243, 2022.
De Marco, A., (2016) Flettner Rotor Concept for Marine Applications: A Systematic Study, International Journal of Rotating Machinery, Volume 2016
Manoeuvre simulations in design process of wind powered vessel
Olov Lundbäck, RISE
Wind propulsion systems (WPS) are one of the most promising technologies for ship propulsion that can radically reduce greenhouse gas emissions. However, attention must be paid to the additional transversal forces and yaw moments connected to a wind propulsion system, as it can affect the manoeuvring and seakeeping performance of a ship. This paper demonstrates how time-domain simulations can be utilised to assess the manoeuvrability of a wind powered vessel to support the decision making, from the early design stage, all the way to testing the control systems, design of Human Machine Interface (HMI) and developing crew guidelines and training.
The manoeuvre simulations are carried out with SSPA’s six degree of freedom inhouse code, SEAMAN-Winds. We present firstly a validation against manoeuvring model tests of a wind powered ship, where the wind propulsion units are represented by pulling fans.
VPP calculations, which are commonly used in the early design phase, can predict the rudder angle required to balance the side force and yaw moment from the wind propulsion system. However, such steady-state computations provide no information on how robust this balance is when dynamic effects are present (e.g., wind gusts) and whether the balance can be regained if it has been momentarily lost. Therefore, time-domain simulations are shown to be useful to assess whether a ship can sail safely close to the limits of its VPP polars.
Furthermore, it is demonstrated how mariners operating a real-time manoeuvre simulation tool can be utilised to increase the proof-of-concept, assess the HMI design, and for crew training.
Building trust in thrust – Technology provider collaboration to open the market for wind propulsion
Jukka Kuuskoski, Norsepower
Interest in wind propulsion technology is growing rapidly and it is expected the market is about to take off. This paper outlines some key hurdles still left for the technology acceptance and proposes realistic “house rule” -principles to improve the trustworthiness of the wind propulsion industry and smoothen the pathway to a wider technology adoption.
These principles are
- Genuine collaboration on regulation
- Zero tolerance on overpromising
- Take safety seriously
- Highlighting the market potential in communication “The ball is already rolling”
The existing rules and regulations are not always written to accommodate wind propulsion. However, there is great regulatory push to improve the energy efficiency of shipping. Wind propulsion has direct fuel saving potential but it can be an economical enabler for alternative fuels. These regulations are clearly a “common ground” on which technology providers can wholeheartedly collaborate.
Nothing harms more the trust in the technology than inflated promises and misleading information. Blatantly wrong claims only slow down the uptake of wind propulsion in general. Wind propulsion has enough potential even without exaggeration.
Shipping is conservative industry and there is a good reason for that. Seamen rely on technology providers to create a safe working environment thousands of kilometers away from the closest shore. Wind propulsion providers need to be worthy of that trust.
Finally, it is noted that communicating the overall potential and the fact that the transition is already happening has capability to accelerate this transition. Emphasis on the wider market potential in messaging should be encouraged.
Empirical methods for developing WASP performance indicators and Heuristics decision making under uncertainty.
Konstantinos Fakiolas, FINOCEAN LTD.
Wind-assisted ship propulsion is recently perceived positively by ship Owners and Operators as one of a potentially promising energy saving and emission reduction direction, however still the acknowledgement of a variability in the wind conditions, the uncertainty about ship trade routing and sometimes even by the complicated performance prediction analysis presented by WASP and WASP performance technology providers, create a lack understanding of the main dynamic functional principles of WASP on the ship, and reluctance in decision making. In fact ship Owners and Operators – including Charterers – need themselves to be able to understand, develop and utilize performance heuristics about the winds, the ship routing, the impact on a given ship type and the various WASP technology performance physical laws, so that they can better communicate with technology providers on basis of common understanding related to expectations about performance and target settings. They primarily need to have independent indicators of empirical nature, in order to use at hand for achieving a fast technical and business evaluation on the ‘ship-systems-trade’ suitability of a given WASP application.
This paper attempts to provide a first set of such heuristic, empirical performance indicators, sourcing from the fundamental rules of wind-assisted ship propulsion functionality, related to the ship type, WASP system type, the wind conditions and routing.
Wind Propulsion towards Zero-Emission Cruise Vessels
Nicolas Abiven, Chantiers de l’Atlantique
There is no one-fits-all solution to decarbonize shipping, but wind propulsion offers the greatest potential of energy gain for one single solution. In this context, Chantiers de l’Atlantique (CdA), a leading shipyard in energy/environment efficiencies through its pioneered Ecorizon® R&D Programme, has developed Silenseas® sailing cruise ship concept featuring the Solid Sail innovative wind propulsion technology. After R&D evaluations of potential technologies with respect to CdA specifications for large wind-powered vessels (i.e. safety, simplicity, ease of use, durability and performances), no solution fitted CdA needs and the Solid Sail solution has been therefore developed in-house. It is composed of large flat sail composite panels hinged together which deform under wind pressure thus generating aerodynamic trust, and mounted on a 74 meters-tall canting rig.
Through 6-year intensive aerodynamic/fluid-structure interaction numerical modelling and experimental analyses, CdA has developed and tested 3 successive Solid Sail versions, from a J80 small-scale version to 1- year commercial operation on Le Ponant cruise vessel and current full-scale 1500 sqm demonstrator. SolidSail solution is now at its final stage of validation with major weight/cost savings achieved compared to the 1st design version together with sturdiness/safety/ease of use demonstrated, industrial pre-manufacturing analyses conducted and an AiP already delivered.
Solid Sail propulsion system will allow cruise vessels to reduce GHG emissions up to 45% compared to similar conventional ships and is applicable to merchant vessels as well (solution already selected for the Neoliner ro-ro ship). First ship orders are expected by the end of 2022 for ship deliveries by 2025.
References: Solid Sail – Chantiers de l’Atlantique (chantiers-atlantique.com)
“Wind Hunter” – The Zero Emission Cargo Ship Powered by Wind and Hydrogen Energy
Kazuyuki Ouchi, Ouchi Ocean Consultant Inc.
In the year of 2018, IMO (International Maritime Organization) decided that the CO2 emission from merchant ships for the international voyage should decrease by 50% within the year of 2050, furthermore should achieve Zero CO2 emission from every merchant ships within the early years in the second half of 21st century. In this paper, an idea of perfect Zero CO2 emission ship by capturing and using the ocean wind energy is introduced.
When a sailing ship which has large rigid wing sails, for example Wind Challenger Sail, navigates in a sufficiently windy sea area, the thrusts from sails are strong enough so that they are utilized to not only drive the ship at the proper speed but also rotate a large underwater turbine at significant speed and torque. The turbine generates electricity which is used for the water electrolysis to generate hydrogen onboard. The hydrogen is attached to toluene with chemical reaction and changed in the form of methyl-cyclo-hexane (MCH), which is in liquid form under ambient temperature and pressure. The MCH is stored in the ship’s storage tank as a liquid organic hydrogen carrier (LOHC). In the case of weak winds when the sails cannot generate sufficient thrust, the MCH is led to the dehydrogenation device. Using the hydrogen generated by the device, the fuel cell works and supplies electricity to the electric motor propeller for the ship’s propulsion and general service onboard. Thus, the ship can navigate at a constant speed regardless of wind speed and direction.
This sailing ship features large telescopic wing sails, motor/generator commonly used as turbine generator and electric motor propeller, water electrolysis device, hydrogenation device, dehydrogenation device, fuel cell, and storage tanks for the toluene and MCH. The concept of this ship isone of the best candidates for a Zero CO2 emission ship, because the system is operated by only wind energy and does not require fossil fuels such as oil and gas.
High-Performance Composite Materials for Wind Propulsion Technologies: Challenges and Opportunities
Thomas James, HexcelFundamentally, composite materials are a good fit for the marine industry: They can be moulded into complex shapes, they are lightweight, and they do not corrode in seawater.
A wide range of these materials are used in the industry, from low-cost fibreglass reinforced polyester in ferry interiors, to high-modulus carbon reinforced epoxies for sailing-yacht masts.
The re-emergence of wind power for shipping brings with it the need for the best of both worlds: High-performance lightweight materials at low cost. Here we can take advantage of the wind energy industry, which preceded wind power by a generation.
In this presentation we look at key material technologies developed for the highly cost-driven wind energy industry, as well as others developed for aerospace and automotive, and discuss how they could be applied to wind propulsion. We look at the global supply-chain of the materials and the geography of manufacturing expertise. We assess pathways towards improved sustainability of high-performance composites, including the use of recycled and renewable raw materials; reduction of embodied C02; reduction of the energy needed to convert the materials into rigid structures; and we look at the latest developments in the end-of-life challenge. We conclude by highlighting that in some wind power concepts these materials are not required – their use may become a costly distraction. But in other cases, they are an enabling technology without which the concept would fail. In these cases, we have wind-energy to thank for the head-start.
Aerodynamic optimization of the eSAIL, bound4blue’s suction sail for wind-assisted vessel propulsion
Alberto Llopis Pascual, bound4blue
The world is facing one of its ever-major challenges: climate change – which will transform our way of living. Shipping industry is not alien to it, driven by the IMO environmental regulations and increasing fuel price. In the 20th-century, diesel engines revolutionized the industry substituting sails. A new revolution is happening: new environmentally-friendly technologies will be implemented on new-era vessels. Funny fact: sails are back to help on this mission.
bound4blue has developed the eSAIL – a high-lift WAPS that uses suction as active control of the boundary layer – which has been installed on two vessels and three additional coming. This technology was developed in the 1980s by the Cousteau Foundation with the work of Lucien Malavard and Bertrand Charrier. These first units were named Turbovoile and installed on Moulin à vent and Alcyone.
The goal of this research paper is to present the outstanding aerodynamic performances of the eSAIL, which exceed, by far, those of the Turbovoile. This improvement has been achieved by combining CFD modelling and wind tunnel testing. Firstly, the CFD modelling was validated against experimental results from Turbovoile. This validated numerical model was then used to improve design through parametric optimization., delivering an increase of up to 205 in lift-to-power ratio a lift coefficient of up to 8.2. These improved results were confirmed in wind tunnel at a Reynolds number of up to 800,000. Following the design optimisation, an eSAIL interference study was carried out to assess the impact of placing two eSAILs very close to each other.
Key Features of ‘Wind Ready’ Retrofit of a Kamsarmax Bulk Carrier
Nick Contopoulos and Baiqian Jiang, Anemoi Marine Technologies (AMT) and Lloyd’s Register Classification Society (China) Co. Ltd
A major consideration for wind assistance installations has been a need for improvement of ship energy efficiency. From January 2023 a driver for such installations is implementation of requirement for measurement of attained Carbon Intensity.
The paper will introduce key features, design aspects and practical issues arising for installation of Rotor Sail wind assistance with reference to a retrofit of a Kamsarmax Bulk Carrier with Anemoi Marine Technologies (Anemoi) Rotor Sails.
A first prototype case of a Bulk Carrier installation of Rotor Sails in Lloyd’s Register Classification was completed in 2018 for MV “Afros” utilizing four (4) Rotor Sails. A secondtwo-phase retrofit installation of Rotor Sails to a Kamsarmax bulk carrier will be described.
The paper will introduce key features of Kamsaramax Bulk Carrier Rotor Sail retrofit as well as practical issues encountered including:
- Key features of Anemoi Marine Technologies (Anemoi) Gen. 2 Rotor Sail
- Description of Rotor Sail installation for recent Kamsarmax Bulk Carrier retrofit case
- Key aspects of integration design for rail-deployed Rotor Sail retrofit installation
- Practical issues arising in a two-phase Rotor Sail retrofit installation from ship regulatory compliance considerations
- Overview of two-phase retrofit installation adopted for Bulk Carrier retrofit case comprising:
- 1st phase “Wind Ready” installation of Rotor Sail integration and Ship regulatory compliance
2nd phase installation of three second-generation Anemoi Marine Technologies Rotor Sails
About the benefit of optimizing both speed and route in wind-assisted ships multi-objective weather routing
Maxime Dupuy, D-ICE Engineering
Optimizing ship navigation with regards to meteorological and oceanographic forecasts is a crucial issue for the marine industry. Depending on the application, some variations of this problem occur: for racing sailboats, the objective is to minimize travel time, respecting safety constraints while for merchant ships the voyage consumption is optimized, respecting trip duration and maximum ship motions.
For each variation of the problem, different approaches have been developed, but a few are general enough to solve all applications and therefore compute route optimization on sailing, motor, and hybrid-propelled ships. This is a topic of interest as wind propulsion is being pushed on the shipping industry by the IMO regulations, to reduce its carbon footprint. In this context, D-ICE is often acting as a third party for shipowners to compare the performances of wind propulsion systems with statistical weather routing. Through these studies, we noticed that weather routing can enhance the expected fuel savings up to a factor of 2.
Various algorithms are available in the state of the art and an important characteristic is the number of control variables taken into account for the optimization. In this study, we aim at quantifying the benefits in terms of fuel savings of the simultaneous optimization of route and speed for motor and hybrid ships. A larger impact can be expected for wind-assisted ships which are more sensitive to the environment and whose sail propulsion is impacted by the apparent wind, which can be modified and optimized with speed optimization.