Warship 2024: Future Surface Combatants
Sponsored by:
Sponsored by BMT, Babcock, Defence SA, ANSYS, and SH Defence, University of Adelaide, ASC and Supported by the RINA Australian Division, Royal Institution of Naval Architects is once again hosting the highly popular Warship International Conference, with the 2024 instalment to be held on 18-19 June 2024 in Adelaide, Australia.
The increasing complex warship design requires an effective engineering assistance, design configuration control, supply chain and inventory management to meet operational requirements. With the introduction of autonomy and disruptive developments such as quantum technologies, could future operating concepts evolve leading to a step change in design requirements. With vessel design lives between 25 and 50 years naval architects need to consider the effects of current and future technological and operational developments now.
The registration is now open! Click “Book Now” to get your ticket.
Before 1 March 2024 | From 1 March 2024 | |
---|---|---|
RINA Member | £800 | £900 |
RINA Non-Member | £900 | £1000 |
Concession
(retired/students etc.)* |
£400 | £400 |
Authors | £200 | £200 |
Additional Authors | £800 | £800 |
* Please note that RINA Student Members can attend the conference free of charge but the ticket availability is limited. If you would like to become a RINA Student Member and register for the event, please contact RINA Events Team at events@rina.org.uk
If you would like to receive more details about the conference when available, please register your interest here.
Preliminary Programme
View the Preliminary Programme - Day 1 - 18th June 2024
Tuesday 18th June 2024 |
||
08.15-09.05 | Coffee and Registration | |
09.05-09.15 | Welcome Address, The Royal Institution of Naval Architects, UK & BMT | |
09.15-09.25 | Kelly Smith, Chief Engineer MFSS, Babcock | |
09.25-09.30 | Karynna Tuan, Application Engineering Manager, Ansys | |
09.30-10.00 | Keynote: Rear Admiral Rachel Durbin CSC, RAN | |
10:00-10:30 | Coffee | |
Session 1 | Stream 1 - Human Factors | Stream 2 - Ship Design |
10.30-10.50 | Impact of human-driven motion criteria on vessel design and the opportunities created by autonomous technologies Peter Hield, DST Group |
The Application of Disruptive Technologies toward Improved Mission Capabilities for safe Launch and Recovery events in Higher Sea Conditions Dr Bernard FERRIER, Syntek Technologies; SETA University of Exeter (UK) |
10.50-11.10 | Enhancing Naval Auxiliaries Through Human-Centric Modular Design: A Long-Term Perspective Andrew Harris, BMT |
The Mate Ship: Rapid Enhancement of Surface Fleet Lethality Gareth Arnold, Naval Construction Branch |
11.10-11.30 | Naval crew size and habitability – where is the future? Michael O'Connor, Taylor Bros Marine Pty Ltd |
Expanded Thought: A Lightly Crewed and Highly Automated Warship Design Dr. Shelley Gallup, Naval Postgraduate School |
11.30-12.00 | Q&A Panel | Q&A Panel |
12.00-13.00 | Lunch | |
Session 2 | Stream 1 – Digital Engineering | Stream 2 - Ship Design |
13.00-13.05 | Peter Davie, General Manager Capability Development, ASC Pty Ltt |
|
13.00-13.20 | Modelling and simulation to contribute towards test, evaluation and acceptance of future radical warships. Matt Hood, Nova Systems |
Hydrodynamic and mechanical interactions during sea boat launch and recovery Frans van Walree, Maritime Research Institute Netherlands (MARIN) |
13.20-13.40 | Enhancing Maritime Asset Structural Management: What can naval & civilian fleets do? Matthew Williamson, Floating Solutions Consulting |
Design for upgrade – managing the platform to combat system interface Joe Cole, Department of Defence |
13.40-14.00 | Machine Learning Approach to Wave Environment and Hull Stress Pattern Identification for a Patrol Vessel Teresa Magoga, DST Group |
Building Australia's Sovereign Ship Design Capability: Lessons Learnt from Navantia Australia’s LMV-M Design James Coleiro, Navantia Australia |
14.00-14.30 | Q&A Panel | Q&A Panel |
14.30-15.00 | Coffee | |
Session 3 | Stream 1 - Survivability | Stream 2 - Structures |
15.00-15.20 | Combat Safety - The role of Vulnerability Assessment and the Purple Fire tool in meeting the Duty of Care in Wartime James Schofield, Survivability Consulting Ltd |
Weight reduction in existing ship designs David Whittaker, BAE Systems |
15.20-15.40 | Survive the Swarm! Warship Vulnerability to Swarming Uncrewed Aerial Vehicle Attacks Josh Neill, QinetiQ |
Towards Optimised Warship Structural Management during Fleet Transition Bruce Cartwright, University of Newcastle, Australia |
15.40-16.00 | Warship Survivability Networks Vincent Capizzi, Systra ANZ |
Optimising the Future Navy Surface Fleet by focusing on producibility, feasibility and other limitations Tim Lee, AMOG and RADM Peter Marshall AM, RAN (Retd.) |
16.00-16.30 | Q&A Panel | Q&A Panel |
16.30-17.00 | General Discussion and Closure of Day 1 |
View the Preliminary Programme - Day 2 - 19th June 2024
Wednesday 19th June 2024 |
||
08.30-09.10 | Coffee and Registration | |
09.10-09.15 | Welcome Address, The Royal Institution of Naval Architects, UK & BMT | |
09.15-09:25 | Mel Slater, Director Maritime, Defence SA | |
09.25-09.30 | Peter Liisberg, Sales Director, SH Defence | |
09.30-10.00 | Keynote: Glenn Callow, Chief Technology Officer, Austal Limited | |
10.00-10.30 | Coffee | |
Session 1 | Stream 1 - LUSV | Stream 2 - Production |
10.30-10.50 | Designing to Survive beyond 2040 Josh Neill, QinetiQ |
Enhancing Future Surface Combatants Through Advanced Ship Design Digital Twins Leonie Wong, SIEMENS DI SW |
10.50-11.10 | Navigating Challenges: Design, Technology and Operational Lessons from Large Optionally Crewed Surface Vessels Jacob Bailey, Austal and Harry Hubbert, Greenroom Robotics |
The importance of docking facility qualification in the post Defence Strategic Review era Matt de Cure, Department of Defence |
11.10-11.30 | Scaling up Maritime Autonomy – Large Uncrewed Surface Vessel (LUSV) Vision Jake Rigby, BMT |
Composite Repairs: Practical ideas for an increase in capability and operability with lessons from the Oil and Gas Industry Jason LeCoultre, Fuze |
11.30-12.00 | Q&A Panel | Q&A Panel |
12.00-13.00 | Lunch | |
Session 2 | Stream 1 – Ship Design | N/A |
13.00-13.05 | Michael Webb, Professor, University of Adelaide |
|
13.05-13.25 | "The Littoral Warfare Challenge" Ed Waters and Caitlin Hoey, QinetiQ |
N/A |
13.25-13.45 | Challenges in Future Warship Design: The Multi-Mission Drone Carrier Rui Nuno Pereira Pinto da Costa, Damen Naval |
N/A |
13.45-14.05 | Optimizing for Mission: Designing the US Navy’s New Bethesda Class Expeditionary Medical Ship Anton Schmieman, Austal USA |
N/A |
14.05-14.30 | Q&A Panel | N/A |
14.30-15.00 | Coffee | |
Session 3 | Stream 1 – Ship Design | Stream 2 - Energy |
15.00-15.20 | Disruptive Innovations for Naval Vessels: A Case Study of the Navantia Australia Kodal Uncrewed Landing Craft Nirman Jayarathne, Navantia Australia |
Modelling to Support Naval Platform Integration of Laser Directed Energy Weapon Systems Christian Rayes, Defence Science and Technology Group |
15.20-15.40 | From UMS to Full Autonomy; Experience from a Complex Warship Programme Alex Walter and Andrew Curlewis, Babcock |
Achieving more with less, an engine builder’s perspective Gary Wilson, Rolls-Royce |
15.40-16.00 | Designing the Multi Role Combat Vessel Integrated Full Electric Propulsion System: Fostering Collaborations For Successful Design Martin Wibawa and Teo Teck Wee, Defence Science and Technology Agency and Robert Edlund, Saab Kockums |
A study into the Energy and Propulsion Systems of Modern Warships Benjamin Steele, BAE Systems Australia - Maritime |
16.00-16.30 | Q&A Panel | Q&A Panel |
16.30-17.30 | General Discussion and Closure of the Conference | |
17:30-19:30 | Drinks Reception |
Hotel Rates
Special hotel rates available for the conference can be found here. If you have any queries or issues booking your hotel, please contact registrations@accommodationlink.com.au.
Speakers
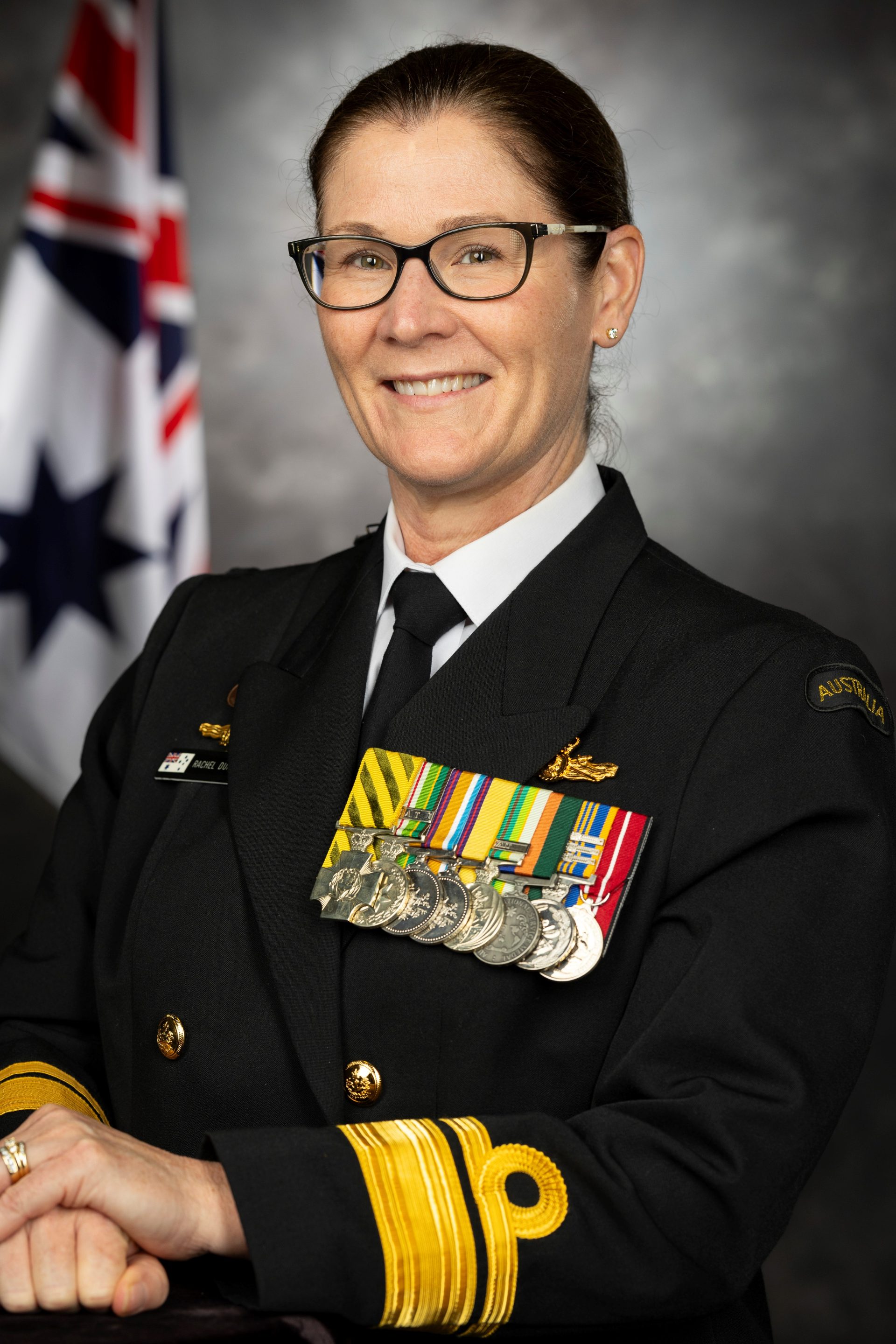
Rear Admiral Rachel Durbin CSC, RAN
RADM Rachel Durbin grew up in the NSW Snowy Mountains and joined the Royal Australian Navy in 1993 through the Australian Defence Force Academy as a Marine Engineer. She spent her sea-time onboard HMA Ships Westralia, Anzac, Canberra and Perth deployed on operations in the Persian Gulf, conducting exercises in North and South East Asia, fisheries operations in the Southern Ocean and border protection off Northern Australia.
Following promotion to Captain in 2013, RADM Durbin enjoyed strategic roles within the Rizzo Reform Program, Major Surface Ships Sustainment (CASG) and Navy Capability Division. On promotion to CDRE in 2021, RADM Durbin served as Director General Engineering—Navy from 2021–2023. In March 2023 RADM Durbin was promoted to Rear Admiral and assumed the role of Head Navy Engineering. She has also served within the Navy Leadership and Culture Program and Navy Workforce Management responsible for engineering workforce requirements and remediation.
RADM Durbin was awarded the Conspicuous Service Cross in 2013. She holds a Bachelor of Engineering (Mechanical), Master in Engineering Management, Master in Arts in Strategy and Management, is a Chartered Engineer and Fellow of both Engineers Australia and the Institute of Marine Engineering, Science and Technology. She is also a graduate of both the Australian Command and Staff Course and the Defence Strategic Studies Course.
She is married to Scott and mother to two active children. She enjoys camping and skiing with family and the relentless pursuit of children’s sports every weekend.
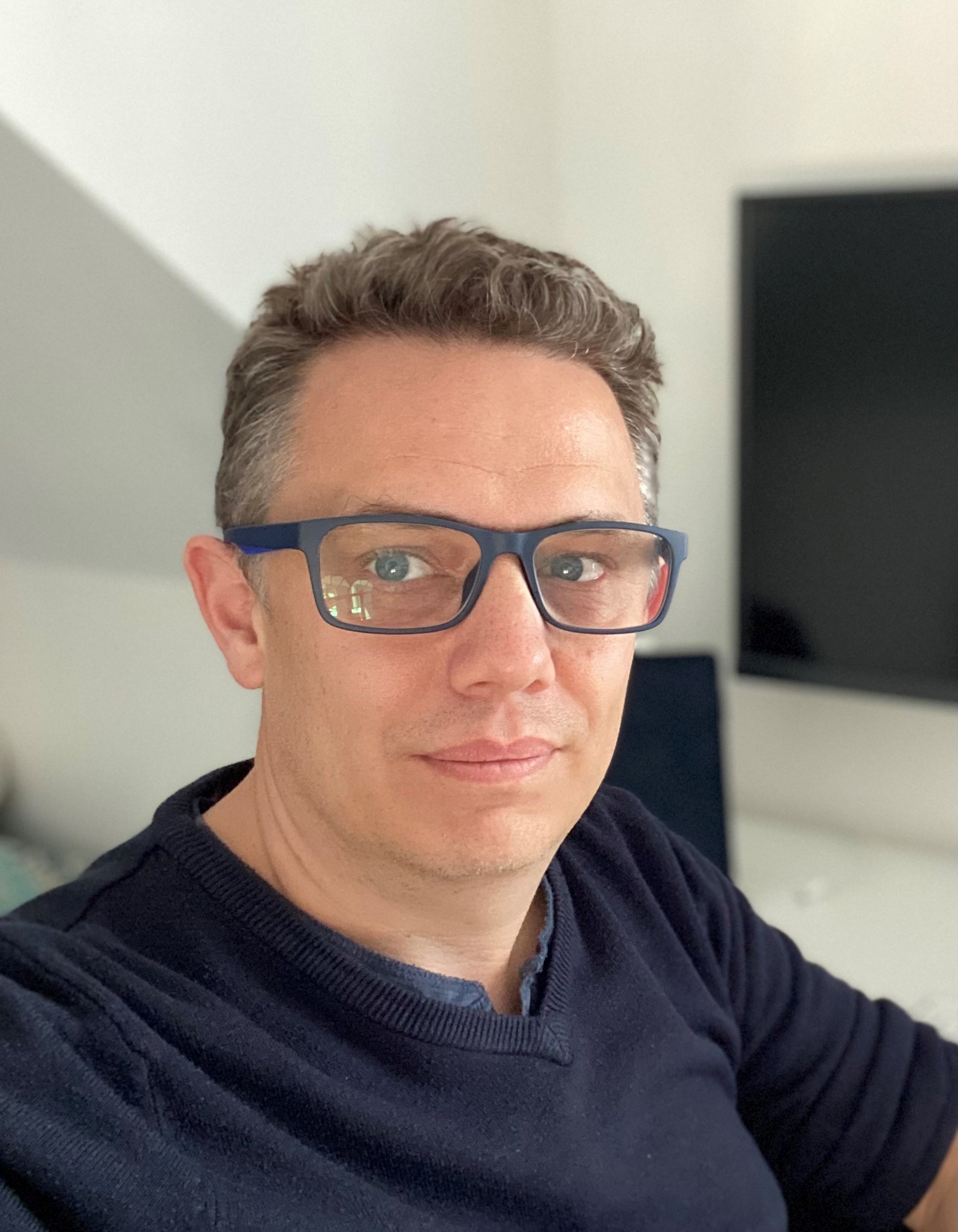
Glenn Callow, Chief Technology Officer, Austal Limited
Glenn graduated in the UK with a Bachelors degree in Computer Science from the University of York and an Engineering Doctorate with Loughborough University. Glenn’s doctoral thesis was focused on novel techniques to improve the Systems Engineering of increasingly Autonomous Systems.
Whilst in the UK, Glenn began his career in the defence sector with BAE Systems at their Advanced Technology Centre (ATC). At the ATC Glenn held a number of scientist positions, becoming Technology Lead for Intelligent Autonomous Systems and Advanced Information Processing in 2010. During his time at BAE Systems, Glenn and his team developed numerous novel robotic and data processing systems for defence customers. This included the advanced demonstrator for the UK’s current generation bomb disposal robot, autonomous mules for supporting dismounted troops and decentralised technologies for improved tracking and situational awareness in the digital battlespace.
Glenn joined Rio Tinto in 2012 and was involved with a significant number of Rio Tinto’s technology developments. This includes the world’s first fully operational deployment of Autonomous Haulage and subsequently scale out, as well as supporting autonomous drills and autonomous rail developments and deployments. He also led the program in Rio Tinto to develop and deploy the world’s first Autonomous Water Truck at Rio Tinto’s Gudai-darri mine, in partnership with CAT. A primary focus of his work at Rio Tinto was the development and deployment of the Rio Tinto Mine Automation System (MAS). This operational digital twin platform, deployed at all of Rio Tinto’s major surface mines, provides a platform for the research, development and deployment of decision automation technologies that enable a broader integrated, automated mining value chain.
In 2023 Glenn joined Austal as Chief Technology Officer. Glenn’s role at Austal oversees a number of technology areas, including:
- Australasia and Corporate ICT services and support,
- Austal Group’s in-house Research and Development,
- Sales and Support of Austal Digital Technology products, such as the Marinelink Control & Monitoring suite and the LUSI Asset Management solution,
- Austal Group Strategy, Commercial Development and M&A.
Topics
The conference will present technical developments in the design, construction, and support of surface ships, including but not limited to the following topics:
- Future Navy Surface Fleet Mix
- Design for constructability and supportability
- Facilities and Shipbuilding
- Automation in Ship Design and Construction
- Digital Engineering
- Use of Offboard Autonomy – Partially or Fully Autonomous Ships
- Disruptive Technologies
Abstracts
View All Abstracts
Please note that the abstract list may be updated later.
Enhancing Naval Auxiliaries Through Human-Centric Modular Design: A Long-Term Perspective
Andrew Harris, BMT
Naval auxiliary vessels are pivotal to maritime operations, expected to operate effectively across decades. However, their design presents multifaceted challenges related to space optimization, durability, and adaptability. This paper advocates for a paradigm shift through the implementation of human-centric modularity in the general arrangement of these vessels, emphasizing versatility, sustainability, and the integration of evolving technologies and services.
Designing naval auxiliaries necessitates incorporating personnel within confined spaces, a challenge further complicated by the modern demand for increased functionalities. This paper proposes a holistic approach that perceives these limitations as opportunities for innovation. Drawing insights from advancements in submarine habitability and adaptive design, it recognises the potential to revolutionise naval auxiliary design. The approach utilises a comprehensive methodology to balance warship design requirements with the essential long-term flexibility.
An illustrative instance of this strategy involves the integration of a modular hospital fit within naval auxiliaries. Inspired by the concept of containerization, reminiscent of server room design, this strategy transitions medical and essential services like victualing from hardware-centric solutions to service-based procurements. This shift acknowledges the necessity for adaptable, efficient solutions across the extended operational lifespan of naval auxiliaries.
Modularity expands beyond physical spaces to encompass supply chains and logistics. Service providers, including medical aid companies, might shift from hardware sales to service provision. This transformation redefines how crucial functions are sourced and integrated into naval operations, significantly enhancing sustainability and adaptability.
This human-centric modular design for naval auxiliaries signifies more than a mere design enhancement. It marks a fundamental paradigm shift in naval operations, offering a dynamic, adaptable, and sustainable model. This model anticipates the ever-evolving needs of maritime defence, enhancing vessel capabilities and ensuring a long-term and sustainable operational approach. This shift holds the promise of reshaping the operational effectiveness and adaptability of naval auxiliaries across their extensive operational lifespans.
Designing to Survive beyond 2040
Josh Neill, QinetiQ
Parallel developments in uninhabited small surface vessels (USV) and ‘loyal wingman’ concepts for combat aircraft suggest that large, uninhabited surface vessels (LUSV) will form a significant element of many naval forces in the future.
Such LUSV could function as distributed sensor nodes and additional magazines in a network of linked combat ships. This form of vehicle offers both opportunities and challenges, one of which is the survival of the LUSV in combat. This paper explores the implications of ultra-low crewing and uninhabited LUSV for vessel security, vulnerability, damage control, repair and recovery. In doing so the opportunities for radically different operating methods are explored alongside the naval architecture issues that will arise as LUSV are designed to break the dependence on human limitations.
The Application of Disruptive Technologies toward Improved Mission Capabilities for safe Launch and Recovery events in Higher Sea Conditions
Bernard Ferrier, Syntek Technologies; SETA University of Exeter (UK)
In piloted aviation, a deck officer normally guides an arriving air vehicle to a safe deck landing. The Deck Officer uses the combination of visual cues and deck behaviour by “feeling the deck” to anticipate the deck’s condition. In automated operations, the approach is different.
One of the most challenging tasks in the deployment of basic ship-based VTOL Uncrewed Air System (UAS) is the launch and recovery and deck handling performance on smaller ship platforms. This is owing to the random nature of seaway. The time needed to set-up an air vehicle from the perch to its recovery may be longer than the deck motion quiescent windows may persist. Quiescent Period Prediction (QPP) objective is to provide ship motion conditions and motion predictions with sufficient forecasted time (over a minute) to launch, recover and complete other motion sensitive tasks regardless of the seaway. The wave radar measured seaway is combined with an artificial intelligent (AI) machine.
Owing to the advance of AI techniques and other technologies, this challenging task is achievable. The initial research demonstrated that owing to the random nature of the sea, AI by itself would not suffice. To furnish the AI machine a stable starting system, the fundamental concept is to measure remote sea surface profiles by wave radar to predict the future wave forces acting upon a vessel. In this research, wave measurements were combined with AI models to predict the next few seconds in near real-time. Test results, which are characterised as encouraging, are discussed.
Towards Optimised Warship Structural Management during Fleet Transition
Bruce Cartwright, University of Newcastle / Pacific ESI
To ensure a surface combatant capability, particularly during the transition between aging and new warships, rigorous assessment of structural service life of naval ships is required. However, such assessment is often based on linear and deterministic methods; the uncertainties regarding the seaway loading, structural configuration, and age-related degradation are implicit. This can lead to unnecessarily conservative maintenance and ship withdrawal decisions. Non-linear and probabilistic analyses enable uncertainties to be taken into account, but tend to be time or cost prohibitive. Thus, tailored approaches, including those employed in digital solutions, are receiving attention.
One solution to characterise the structural response of an aging warship in a seaway is coupled Smoothed Particle Hydrodynamics – Finite Element Analysis (SPH-FEA). Initial validation of a novel implementation of SPH-FEA to predict the complex interaction between surface waves and a frigate, by comparing experimental heave and pitch motion responses and vertical bending moments at forward speeds in regular waves, has been completed. To mature the SPH-FEA approach, refined modelling of the fluid (smaller SPH particles) and analyses at a limited number of critical operational conditions are needed.
This paper presents the next phase of validation of the SPH-FEA implementation. The paper also presents a case study to demonstrate the utility of SPH-FEA combined with improved definition of the hull structural elements considering degradation due to corrosion. The benefits of this predictive capability include reduced maintenance costs, whilst ensuring that aging naval ships can be operated safely beyond their originally planned lifetime.
Impact of human-driven motion criteria on vessel design and the opportunities created by autonomous technologies
Chris Borkowski, Defence Science and Technology Group
The design of large uncrewed vessels intended for the support of naval warships offers the potential to be free from human driven motion criteria. Such criteria include Motion Sickness Index (MSI), Motion Induced Interruptions (MII) and green water limits which are introduced to ensure the safe and efficient execution of tasks whilst at sea. Combined with equipment driven criteria such as ship slamming limits and vertical velocity at the flight deck, all these criteria have an effect on the vessel’s operability and therefore influence the design of the vessel.
With the on-going advancements in autonomous technologies and automated systems, the feasibility of a large uncrewed surface vessel to support naval operations is continuously improving. To both understand and exploit the opportunities created with the removal of human-driven criteria in the design of the hullform a Design Space Exploration (DSE) activity has been conducted utilising the modelling and simulation framework, InteShip, which is currently being developed by Defence Science & Technology Group (DSTG).
This paper presents a study that explores the DSE for warship support vessels designed with and without the consideration of human driven vessel design regulations for a range of selected vessel parameters. The study was conducted using InteShip to calculate vessel parameters and determine vessel performance. Study outcomes have identified the trade-offs between these selected vessel parameters that can be applied to vessel design.
Modelling to Support Naval Platform Integration of Laser Directed Energy Weapon Systems
Christian Rayes, Defence Science and Technology Group
Directed energy technologies, specifically high energy laser systems, are continuing to be developed within industry and academia to address commercial and military needs. Navies are considering the integration of these systems into their anti-air capabilities, giving them another effective option to deter and neutralise an ever-increasing threat from unmanned aerial systems and other airborne weapons.
Naval vessels are intricate amalgamations of integrated systems, including platform, power, propulsion, combat, and communication systems. The seamless functioning of one system significantly influences the performance of others. This interconnectedness creates a dynamic equilibrium, where the vessel’s physical structure, energy distribution, combat capabilities, communication networks and other systems are interdependent, shaping the ship’s overall operational effectiveness.
A comprehensive understanding of how different laser output powers perform in various threat engagement scenarios is important, but how the placement and size of the required batteries impact the seakeeping ability of the platform is also crucial for naval ship designers. The dynamic behaviour of the ship can have a significant effect on a weapon’s accuracy and effectiveness. This paper delves into the integration of high energy laser systems in naval anti-air capability, exploring variations in performance and their corresponding space, weight and power requirements.
Leveraging modelling and simulation tools, this study assesses the implications on ship stability, seakeeping, operability and range, providing valuable insights for effective implementation and operational success.
"The Littoral Warfare Challenge"
Ed Waters and Caitlin Hoey, QinetiQ
Advances in anti-access and area denial weapons are challenging the ability for navies to carry out traditional amphibious operations. In turn this is driving research into technologies, equipment, systems and concepts of operation to overcome these threats to ensure that it remains possible to project power ashore from the sea. The combination of threat environment and adoption of technology and practice inevitably means that ship designers will need to look long and hard at new equipment, systems and even the overall configuration of the next generation of amphibious shipping. This presentation will provide an overview of how some of these issues might be approached over the coming years.
The Mate Ship: Rapid Enhancement of Surface Fleet Lethality
Gareth Arnold, Naval Construction Branch
The current RAN surface fleet is well-equipped in sensor and combat management systems but lacks the ability to deploy sufficient effectors for high-end warfare.To overcome this capability gap, a class of vessels could be constructed based on existing high-speed wave-piercing catamaran designs to act as additional missile magazines for existing fleet units. These vessels would provide enhanced lethality to the RAN in a short timeframe, at low cost, with small crew requirements and could be built by Australian shipbuilders based on existing designs. This presentation covers the operational concept and conceptual design of such a vessel.
Achieving more with less, an engine builder’s perspective
Gary Wilson, Rolls-Royce
This paper will examine the challenges and opportunities around electrification, environmental sustainability and digitalization in future warships, especially in respect of power and propulsion systems, and consider how these both require and assist shipbuilders and navies in achieving more with fewer resources.
Warships have embraced electrification more quickly than in other sectors because of military and operational benefits and flexibility of ship layout, and with missions systems requiring more electrical power that can often involve large transients, this trend is likely to continue. This paper will revisit these benefits before considering how design options such as variable speed generation, energy storage and control design can help to supply these newer demands.
Alternatives to fossil fuels, such as biofuels and synthetic fuels, are also growing in prominence across the global economy as the world seeks to transition to a more sustainable future. While these generally have economic and energy density costs that navies would have to adapt to, their adoption may be more a necessity than a choice if traditional fuels become less available. This paper will discuss upcoming trials of such fuels as well as ship design and operation options to help to mitigate the impact of transitioning.
Digitalization is a broad term that encompasses a wide range of data acquisition, transmission, storage and processing applications. This paper will focus on its application in helping the design of warship power systems to optimize asset availability and also handle new mission system loads and to address other challenges such as emerging missile threats and reduced crew numbers. This will include control options for handling transients and for enhancing resilience and endurance under a range of operating conditions.
Austal’s Design for Constructability & Supportability
Gopinath Sugumaran, Austal Ships
In the world of ship building, a few novel factors from the design and construction phases can unfold a butterfly effect upon the commissioning and sustainability stages. As a good practise, rule of thumb is to implement any of these lessons learnt back into the design phase to better improve the final product. In the real world however, this can be a challenging process as most of the organisations involved in ship design do not end up constructing or maintaining the vessel through its service life.
The invaluable experience gained through in-service support has positively benefitted Austal as an OEM to apply any improvements identified back into the design phase with ease for better constructability & supportability. This paper studies and outlines the areas that should be focused on in detail during the design and construction phases in order to create a streamlined supportability in-service - which in turn can assist in the resolution of any unforeseen challenges faced by the Australian Naval Shipbuilding Industry.
Scaling up Maritime Autonomy – Large Uncrewed Surface Vessel (LUSV) Vision
Jake Rigby, BMT
The naval landscape is evolving and so must our operating strategies. Whilst the concept of a Large Uncrewed Surface Vessel (LUSV) is not new, many navies debating their future fleet composition have yet to formally consider the use of these types of high endurance vessels to enhance its surface fleet. By making the vessel large you unlock greater capacity and capability as well as ensuring it can be a truly deep water vessel operating all year round in the highest sea states. In order to fuel the debate and discussion BMT has outlined a vision for an autonomous future with the potential of adding mass to an existing or future fleet. When considered within a mixed fleet approach, the LUSV demonstrates compelling technical feasibility. However, as we chart this course towards the future of naval capabilities, it will be imperative that we further explore the economic viability to ensure a balanced and sustainable naval strategy.
This paper outlines a vision for an adaptable, affordable and autonomous vessel of the future for discussion. Focusing on the six key challenges of command & control, sensor data management, low carbon engineering systems, vessel & mission resilience, maintenance & logistics and modularity; this paper outlines the potential benefits and creates a technology roadmap of the developments required to turn the vision into reality.
From UMS to Full Autonomy; Experience from a Complex Warship Programme
James Johnson, Babcock International
The Type 31 Frigate has been optimised to reduce Ship’s Company, delivering the required operational capability whilst ensuring personnel safety and supporting personnel retention. The design adopts the latest in engineering solutions, such as the first use of the UMS notation in a Royal Navy warship and a Mission System that automates the process of compiling the common operating picture.
The paper will explore critical design features observed during the development of a lean crewing solution for a class of ships currently in build, providing insight in future design effort and the adoption of technology solutions that enable trade-offs between cost, functionality and complexity on the path to increasing levels of platform autonomy.
This paper will also discuss recent experience gained from other programmes and current research activity that contribute to solutions for crewing needs today, but also provides a feasible pathway to full autonomy in the future.
Combat Safety - The role of Vulnerability Assessment and the Purple Fire tool in meeting the Duty of Care in Wartime
James Schofield, Survivability Consulting Ltd
The concept of Combat Safety addresses issues raised in UK Supreme Court rulings that there exists a legal Duty of Care to service personnel in wartime. It delivers a structured process to execute and record the survivability design process of a warship. Survivability is defined as “The capability of a weapon system to continue to carry out its designated mission(s) in a combat threat environment”, and in this case it refers to the ability of the warship as a whole to protect its crew and the systems that they rely on to keep the ship fighting. Survivability is a function of susceptibility (the probability of being hit), vulnerability (the probability of being disabled when hit) and recoverability (the probability of rectifying the disability after being hit). Of course, it is preferable to not be hit, but this is impossible to guarantee. Of the three areas, arguably vulnerability management has the greatest impact on whole-ship design, in terms of the benefits to be gained if considered at every stage of the design process. The assessment of vulnerability throughout a design is a well-established process which pre-dates the Combat Safety concept, but is given even more importance because of it. This paper explores Combat Safety and vulnerability management in detail, including the capability of the Purple Fire tool and examples of its use.
Hydrodynamic and mechanical interactions during sea boat launch and recovery – validation of time domain panel method predictions
Frans van Walree (Maritime Research Institute Netherlands (MARIN), Wageningen, the Netherlands)
Daniel Sgarioto, Junghoon Lee, Jenny Mathew and Peter Graham (Defence Science and Technology Group (DSTG), Melbourne, Australia)
Launch and Recovery (L&R) operations in harsh seaway environments present considerable risks to materiel and personnel largely due to the hydrodynamic and mechanical interaction forces that develop between dissimilar-sized vessels when operating at speed in close proximity. The development and validation of computationally efficient numerical tools, capable of predicting both hydrodynamic and mechanical-based interactions during L&R, offers the potential to greatly enhance capability for these operations and the safety of personnel and materiel involved. These tools can be readily used to develop operational guidance materials for specific combinations of parent vessel and deployed system of interest.
Limited validation studies have been published on the numerical predictions of multi-vessel interactions during alongside sea boat L&R evolutions. One example is Van Walree et al (2018) where the PanShip time domain panel method was validated for sea boat (RHIB) motions while towed alongside an offshore patrol vessel (OPV). The present paper goes a step further to validate the weakly nonlinear version of the PanShip method for sea boat L&R including alongside towing as well as lifting and lowering of the sea boat by means of a crane. Using model-scale data from tests performed in MARIN’s Seakeeping and Manoeuvring Basin, PanShip simulations were performed to validate several aspects of a typical alongside crane-based L&R scenario, including sea boat motions and acceleration levels; and tension forces in both the painter and lifting/lowering lines. The simulation tool predicted with acceptable accuracy all relevant seakeeping characteristics that influence alongside L&R operability, once experimentally derived tuning was employed.
Design for upgrade – managing the platform to combat system interface
Joe Cole, Department of Defence
Combat systems and platforms have very different refresh cycles. This paper explores the use of design modularity and spatial arrangement to manage the combat to platform system interface and reduce the burden of combat system refresh. The work focuses on surface combatants and seeks to balance the capability of the integrated ship system in aspects such as topside design, survivability, ship performance and growth margins. The retrofit of new combat systems to existing ship designs creates many design challenges and necessary compromises. This work identifies design options available in a new platform design to accommodate current and future combat system needs. The aim is to reduce the cost and time associated with mid-life upgrades and increase the likelihood of a surface combatant design being compatible with long multi-flight build programs. The work considers examples from past programs and literature as well as presenting a set of exemplar surface combatant spatial designs and design features.
Survive the Swarm! Warship Vulnerability to Swarming Uncrewed Aerial Vehicle Attacks
Josh Neill, QinetiQ
As the 21st century progresses, Uncrewed Aerial Vehicles (UAVs) continue to gain popularity for navies modernising their forces and this trend is likely to continue. While these new technologies aim to enhance the capabilities of naval platforms, the ability to endure the threat posed by attack from such craft is also being considered. This paper aims to analyse likely outcomes of a swarming UAV attack against a surface warship, with support from the Survive software, to identify lessons in survivability for warship design.
A key difference between swarming UAV attacks and traditional anti-ship missile attacks is the number of hits that a vessel might be expected to receive. The swarm may overwhelm the anti-air warfare systems of a vessel in a way that small numbers of missiles do not, leading to multiple, near-simultaneous weapon strikes being delivered to a single ship.
Survivability principles of redundancy and separation, as well as concentration and protection are typically geared towards damage from a single threat weapon. How such measures fare in the context of multiple weapon strikes is explored through modelling the vulnerability of a generic frigate using the Survive software.
Designing the Multi Role Combat Vessel Integrated Full Electric Propulsion System: Fostering Collaborations For Successful Design
Martin Wibawa, Defence Science and Technology Agency
During an 18 months period, an on-site, fully integrated project management team consisting of customer, designer, builder, and end-user, completed a DNV certified basic design of Singapore’s new Multi Role Combat Vessel (MRCV). The MRCV is a new ship class in the Republic of Singapore Navy, being designed as a mothership for unmanned systems with an extensive ability to support unknown future upgrades. Traditionally, naval design programmes are associated with long lead times and schedule delays; but with focus on some key management elements, such as transparency and collaboration, the team navigated through various challenges to deliver the basic design within a challenging timeline. By exemplifying the design development of the MRCV Integrated Full Electric Propulsion system, the paper explains the required management and leadership applied by the project team fulfilling the vision of the Singapore MRCV.
The importance of docking facility qualification in the post Defence Strategic Review era
Matt de Cure, Department of Defence
In the modern era naval platforms are continually becoming larger, more complex, and significantly more expensive. The resource investment required to design, build, and maintain naval platforms has made it such that warships and other craft can take years or even decades to go from blank paper to a deployable capability. Due to this resource requirement, it is important to ensure that the platforms that are being built, and maintained while in service, are protected as best as possible from any inadvertent damage.
With the renewed focus on the navy and the naval force structure following the Defence Strategic Review every naval hull is of importance to the fleet. Use of the RAN’s docking facility qualification program will minimise the risk that sea days, or whole platforms, are lost to avoidable accidents involving docking infrastructure. This will be especially vital as Australia moves into the nuclear era, where we are performing maintenance on the nuclear submarines of other navies and in time on our own.
The robust qualification process developed by Navy Engineering Branch, which has been implemented with the help of the Collins Submarine Program in the submarine domain, ensures that materiel standards of docking facilities is maintained. As the continuous naval shipbuilding program ramps up, and new docking facilities are brought online to support nuclear powered submarines, the qualification process will support the safe docking and undocking of RAN vessels without the repeat of accidents of the past.
Modelling and simulation to contribute towards test, evaluation and acceptance of future radical warships.
Matt Hood, Nova Systems
In 2015 I presented a paper to the RINA Warship conference entitled 'The Shape of Fleets to Come'. That paper was based on historical analysis of the shape of naval fleets and looked forward to 2045. The paper concluded with a look at radical platforms for future warships. This paper starts from the premise that radical platforms will be proposed and examines the challenges with test, evaluation and acceptance that arise when traditional rule-based acceptance and safety assurance, proven by sea trials are inadequate. In particular, we know that offboard autonomous systems are going to be used in all domains and for many types of missions.
The paper will draw on Nova Systems’ work on modelling and simulation of ship-air interfaces and work on ship-to-boat interfaces and combine this with our experience of aviation integration, testing and safety assurance that has moved towards autonomous systems and manned-unmanned teaming. We will explore how a radical new concept platform can be assured progressively throughout its lifecycle to deliver operational capability faster than traditional warship procurement processes. The target radical platform will be a multi-hull platform for operating offboard crewed and uncrewed systems in air, surface and underwater environments. This future surface combatant platform is constructed from hybrid composites and designed to be ultra-modular with many systems embedded in ISO containers to enable evolution through life and flexibility for different missions.
Nova is an independent adviser on integration, test and safety, we are not tied to any particular product, design or manufacturer.
Composite Repairs: Practical ideas for an increase in capability and operability with lessons from the Oil and Gas Industry
Jason LeCoultre, Fuze
Composite repairs in a marine environment have been a practical reality for the past 30 years. They have been applied in a wide range of commercial and Naval Applications with varying rates of success. Given the potential to increase capability and availability of naval assets, this paper seeks to synthesise past experience, provide details of how the repair process can be optimised, detail where composites can be successfully implemented and provide concrete examples and case studies. This paper also provides a summary of organisational best practice required to successfully implement an optimum repair using composites.
Enhancing Maritime Asset Structural Management: What can naval and civilian fleets do?
Matthew Williamson, Floating Solutions Consulting
The use of digital visualization and modelling has made significant progress in the last few years, there is now a huge amount of data that can be generated using a wide range of digital methods. Effective display, use and manipulation of this data can be costly and may not provide a return on investment. However, harnessing this data in a manner that enables structural optimisation to be simpler and easier can be a powerful enabler for through life support.
Using lessons learnt that apply equally to naval and civilian assets, this paper illustrates some practical ways that this spectrum of technologies and the resulting data can be harnessed at a working level.
Building Australia's Sovereign Ship Design Capability: Lessons Learnt from Navantia Australia’s LMV-M Design
Nirman Jayarathne, Navantia Australia
The development of sovereign ship design capability is essential for Australia to ensure its national security and economic prosperity. It allows Australia to design and build ships that meet its unique operational requirements, reduce its reliance on foreign ship designers and shipbuilders, grow the local Defence industry by creating and sustaining new jobs, and boost the economy.
The Navantia Australia’s LMV-M design is a significant milestone in the development of Australia's sovereign ship design capability. The bespoke design leveraged best design practices proven by the in-service Landing Craft (LLC) to meet the new and challenging requirements of the Australian Army. The design features several innovative features such as semi-autonomous operation capability and Unmanned Aerial Vehicle (UAV) integration.
This paper will examine the development of Australia's sovereign ship designs using the Navantia LMV-M design as a case study. First, it discusses how to develop well-defined roadmap for the development of the capability that aligns with the requirements. Second, when, and how to involve the key stakeholders in the development process. Third, how, and where to invest in research and development to ensure that the design contains the cutting-edge technology. It then discusses the key stakeholders involved, the key milestones achieved, the key elements of the capability, and the lessons learnt that can be applied to the future. The paper will conclude by discussing the future of Australia's sovereign ship design capability and the opportunities and challenges that lie ahead.
Disruptive Innovations for Naval Vessels: A Case Study of the Navantia Australia Kodal Uncrewed Landing Craft
Nirman Jayarathne, Navantia Australia
Uncrewed landing crafts (ULCs) offer a number of advantages over traditional landing crafts, including increased survivability, reduced cost, and enhanced capabilities. They can operate in hazardous environments, conduct missions that would be too difficult or expensive for manned landing crafts, and revolutionize naval warfare.
Navantia Australia (NAUS) has developed the Kodal ULC, a high-speed, high-payload ULC designed to operate in a wide range of maritime environments and perform various missions. NAUS's experience developing the Kodal ULC provides valuable insights into the challenges and opportunities of disruptive innovation in naval ship design.
Some of the key challenges that NAUS faced in developing the Kodal ULC included developing robust and reliable autonomous navigation and control systems, designing a ULC that is capable of operating in a wide range of maritime environments, and ensuring that the ULC is compatible with existing naval logistics and support systems. NAUS successfully overcame these challenges and developed a cutting-edge ULC with the potential to revolutionize naval warfare.
This paper examines the development journey of the ULC by NAUS, focusing on the key drivers and enablers of the Kodal ULC development program, the key technological challenges that NAUS faced and how they were overcome, and the potential operational impact of Kodal ULCs on naval warfare. The paper concludes by discussing the future of disruptive innovations for naval vessels and the opportunities and challenges that lie ahead.
Challenges in Future Warship Design: The Multi-Mission Drone Carrier
Rui Pinto da Costa, Damen Naval
In recent years, a surge of the use of unmanned vehicles in military operations has been observed, with particular relevance in the naval domain. The aim of this work is to explore the operational potential of the application of these systems in a naval surface warship, engaging with the naval architecture and design challenges associated with this endeavour and developing tools to assist in the concept design of drone carrier ships. To do so, the conceptual design process of a drone carrier warship will be developed, with a multi-role operational concept and requirements comparable to modern European NATO (North Atlantic Treaty Organization) navies. This conceptual design process will include the overview of the state of the art of surface warship preliminary design methodologies as well as of the drone carrier ships themselves, the development of an operational concept for the ship along with the definition of its operational requirements, a system selection process in which the systems that the ship will make use of in order to undertake its wide range of missions will be defined, the development of a ship synthesis model and, finally, the development of two ship concepts for different NATO end-users. The final conceptualized vessels, when detailed and analysed, were found to merge various characteristics from both modern surface combatant ships such as frigates, destroyers and cruisers as well as conventional carrier warships. The operational potential of these ships, when considering the need for future-proofing modern warships, is particularly high as the main vessel’s purpose is to serve as a platform for multi-role unmanned vehicles - which can be upgraded throughout the life cycle of the ship without the need for large refit periods – as well as the need for platforms that are exceedingly operationally versatile in order to tackle constantly changing threats and challenges in the modern naval battlefield.
A study of the effects of defect size, type and position in friction stir welded steel for marine applications.
Stephen Cater, TWI (The Welding Institute)
Friction stir welding (FSW) was invented and developed for fabricating difficult to weld metals such as aluminium in the 1990’s by The Welding Institute (TWI). FSW is a solid state joining process that gives high strength, tough, fatigue resistant welds with minimal distortion and so was quickly adopted by the shipbuilding sector for fabricating the aluminium superstructures of commercial shipping and the complete fabrication of high speed ferries, fast attack craft and small naval vessels. Transferring the technology to the fabrication of steel was always seen as desirable but was frustrated for almost three decades by the difficulty in developing a FSW tool that can withstand the higher temperatures and forces associated with welding steel. This has now been achieved and work is underway to adopt the process for the fabrication of steel ships.
Though FSW typically produces welds with excellent properties which, in steel, are not only better than those of traditional arc welding but usually considerably improve upon the parent metal properties, an important part of the work reported here is a consideration of the types of defects that can occur in friction stir welding and their potential influence upon the properties of the fabrication.
The possibility of combining both FSW and Submerged Arc Welding (SAW) to create a hybrid process utilising the best features of both techniques to provide high productivity and a fully forged, defect free weld microstructure will also be considered.
Machine Learning Approach to Wave Environment and Hull Stress Pattern Identification for a Patrol Vessel
Teresa Magoga, Defence Science and Technology Group
Defence and patrol vessels are purpose-built, and are required to operate in harsh ocean conditions and demonstrate operational reliability. To support the structural management of defence and patrol vessels, instrumented hull monitoring systems have been deployed. Such systems can provide an abundance of ship performance data related to the encountered wave environment, and in turn a basis for the exploitation of data-driven solutions. One data-driven approach is machine learning (ML), which is a subset of artificial intelligence algorithms that learn how to form decision boundaries to classify or predict data as belonging to a pattern within the dataset.
This paper presents an exploratory study on the identification of patterns in the relationship between the wave environment and hull stresses in a coast guard cutter, through the development and application of a ML framework. The dataset comprises strain measurements from a hull monitoring system installed on the cutter coupled to hindcast wave parameters, including significant wave height and wave period. The open-source SHapley Additive exPlanations (SHAP) library has been used in the ML framework as it enables the identification and “explainability” - or determination of the relative importance - of the interactions between input variables on the output. Patterns in the wave parameters that correspond to relatively high stresses were successfully identified, indicating that further development of the ML framework is warranted. Accordingly, the paper concludes with recommendations to aid the structural assessments of defence and patrol vessels.
Warship Survivability Networks
Vincent Capizzi, Systra ANZ
This study addresses the strategic investment in warships by Australia, emphasizing the imperative for optimal survivability within budgetary confines. 'Survivability,' synonymous with effectiveness and capability, is underscored by US legislation, including US CFR Title 10 Section 2366, mandating realistic threat-based testing for surface ships and submarines.
Naval ships, unparalleled as systems of systems, pose intricate engineering challenges marked by fragmented design information, diverse analytical systems, and varying levels of accuracy. Survivability, reliant on integrated systems and design cohesion, spans the entire product design life cycle.
Graph Theory proves instrumental in comprehending networked, distributed, and interdependent systems. Introducing visual nodal concepts and quantifying connectiveness and interdependence, it becomes pivotal in shaping architectural features like robustness (survivability).
The application of "clustering" in physical systems analysis, driven by Graph and Percolation theory, emerges as a determinant of survivability. Analysing system evolutions through multilayer network structures provides insights into interactions at various levels. System topology tracks the evolution of interactions, especially during subsystem breakdowns.
Survivability, as gleaned from system distribution analysis, hinges on early architectural decisions, facilitating informed choices among alternatives. Robustness becomes evident, offering clarity to decision-makers seeking to optimize warship survivability within budget constraints. This research contributes nuanced insights into warship survivability through a structured Graph Theory analysis.
Keywords: Warship survivability, Graph Theory, Systems of Systems, Percolation Theory, Multilayer Networks, System Topology, Robustness, Naval Design.
Case study: simulation of the shipbuilding process.
Yegor Butenko, ASC Shipbuilding - BAE Systems Maritime
BAE Systems Maritime Australia has developed a digital manufacturing shipyard twin, playing a central role in connecting business functions such as Operations, Engineering and the Project Management Office together.
The shipyard digital twin has been designed to enable rapid creation of shipbuilding scenarios, facilitating daily shipyard capacity analyses, assessing facility investments, and aiding delivery of critical naval capability.
Building upon the foundation of the ship’s digital twin, shipyard digital twin leverages discrete event simulation systems and integrates data from various tools and applications, including ship technical data, ship build strategies, and scheduling information.
The embedded programmable logic within the simulation enables effortless manipulation of big data, effectively reducing manual scenario analysis time from weeks to minutes.
The shipyard digital twin empowers users to easily adjust process variables in ship construction, offering near-instant insights into how these changes impact ship delivery. This model enables the advantage by visualizing the construction process, providing utilisation information and delivering a clear understanding of shipyard constraints without the laborious traditional significant data reviews.
Case study - Delivering a shipyard ready for the future.
Stephen Jelfs, BAE Systems Maritime Australia
In 2017, the CoA contracted Odense Maritime Technologies (OMT) to refresh the design of the Osborne South Shipyard. The refresh added capability for a vertically integrated shipyard enabling a steel in, ships out philosophy. Among the upgrades was significant investment in welding automation for the shipbuilding fabrication hall and large industrial sheds with large capacity cranes to ensure consolidation works could be completed in a controlled environment. As the end user, BAE Systems Maritime Australia has drawn on its experience and lessons learnt from other programs and shipyards, including international reach back, to further develop the vision of a world class surface combatant shipyard at Osborne. An integrated working group including BAE, Australian Naval Infrastructure (ANI), Naval Construction Branch (NCB) and the Commonwealth work collaboratively to deliver a Hunter capable digital shipyard. To support Continuous Naval Shipbuilding (CNS) and a growing shipbuilding community, we are challenged to develop and deliver shipyard infrastructure to accommodate multiple surface combatant platforms in both ship build and repair. The approach is to modernise existing infrastructure and provide new buildings, services and equipment to support fabrication, unit consolidation and outfit, blast and paint and overall block consolidation. Opportunity exists to position key capability in the shipyard to streamline product workflow and to insert advanced manufacturing capability at various stages of the build to address safety, quality, operational hazards, issues and challenges. The introduction of welding automation has seen a significant reduction in safety incidents through a decrease in manual handling and protection from direct exposure via guarding, presence sensing devices and machine interlocks, in addition to the cost and quality improvements.
Optimising the Future Navy Surface Fleet by focusing on producibility, feasibility and other limitations
Tim Lee, AMOG and RADM Peter Marshall AM, RAN (Retd.)
The Future Navy Surface Fleet mix will largely be developed to detect, classify and engage (where appropriate) multiple targets, but if these capability requirements are not appropriately balanced with n producibility, feasibility, and maintainability considerations, the delivery and performance risks will be manifestly elevated. A fleet with too narrow a focus can leave Australia vulnerable to secondary scenarios, thus reducing the likelihood of the Navy being able to fulfil its mission objective; to fight and win at sea. Conversely, by having a diverse fleet with different types of ships and associated capabilities, the Navy increases its overall capability and likelihood of mission success, but at the cost of increased complexity of production, operations, crewing, training, and maintenance. In this paper, AMOG will investigate these increased complexities and summarise the producibility of differing fleet scenarios, tailored to match the strategic fleet review’s recommendations, so that Australia can better understand what is feasible and where the limits of producibility arise. Key aspects investigated will include: • the industrial work force size (including low and high growth allowances), • crewing the ships and associated training lag times (including Naval recruitment low and high growth boundaries), • Opportunities for uncrewed systems and for automation, • approximate costs and build timeframes for the selected recommended ships (based on the strategic fleet review), and • building throughput capacity of the shipyards in Australia (taking consideration of their present work orders and other upcoming shipbuilding programs such as LAND8710) and whether other arrangements (such as building some platforms internationally) may be optimal.
Weight reduction in existing ship designs
David Whittaker, BAE Systems
With tightening budget constraints faced by both governments and navies, modern combatants have service lives that are measured in decades. However, they must defend their countries’ maritime borders and offshore assets in a political climate that can change weekly. With an ever-evolving political climate come new potential adversaries, bringing with them new unanticipated levels of technology. With a combatant’s replacement lead time measured in years, coupled with limited funds, the only affordable response often is to upgrade existing vessels. However, with a finite number of vessels available, and each with a finite displaced volume, there is only so much capability that can be added without the need to take something else off. The challenge for designers, therefore, becomes ascertaining what to take off and from where, so that the ship does not become too heavy. A typical response to this dilemma is to form a committee of subject matter experts to brainstorm what might be removed or replaced with something lighter, so as to make room for whatever weapon or sensor is now urgently required. While this approach will typically find some way of accommodating the required capability, it does not promise the best solution nor is it likely to keep up with a rapidly changing threat landscape. This paper looks at a simple method of scoring entries in the vessel’s weight report to identify likely areas in a ship’s design that will provide maximum weight savings as a means of objectively identifying areas in the vessel’s design to concentrate the design team’s effort.
A study into the Energy and Propulsion Systems of Modern Warships
Benjamin Steele, BAE Systems Australia - Maritime
Modern warships are increasingly complex, so much so that their development is often a joint effort between multiple companies and/or countries. War-fighting effectiveness continues to be challenged by evolving threats and customers are, naturally, seeking increases in capability with little to no impact to the platform – to counter those threats.
The inexorable advancement of on-board combat management systems and combat effectors translates to increases in size, weight and energy consumption, each placing considerable demand on the platform, but particularly on the Energy and Propulsion Systems. Platforms are increasingly being equipped to excel in multiple roles, with payload modularity and platform scalability a new challenge.
This paper describes the state-of-the-art in Energy and Propulsion across the current and emerging surface warship fleets of western navies, and makes an argument for the substitution of the traditional Power with a holistic Energy paradigm. The paper applies parametric comparison and industry intelligence, all from public domain, and identifies novel and emerging arrangements and technologies to meet the Energy and Propulsion System demands of the modern warship.
Mechanical propulsion arrangements, hybrid and all-electric drive systems, manufacturing methods and emerging propulsor technologies are discussed. Energy efficiency, energy management, emerging fuels, thermal and electric storage opportunities, alternative electrical architectures, vulnerability and redundancy of systems are also explored.
This study is essential knowledge for Engineers and Naval Architects developing concepts for new or upgraded warship platforms, and for customers establishing achievable, balanced requirements to ensure war-fighting effectiveness of the platform in its role (or roles).
Naval crew size and habitability – where is the future?
Michael O'Connor, Taylor Bros Marine Pty Ltd
What is the optimum crew size for a modern surface combatant? Habitability standards on surface ships have changed over the years with an increased focus on crew welfare, space and well-being. These standards potentially drive a reduction in crew size.
This is not often reflected however in reality as major warships are increasing capability on the same platform with warships becoming more multi-functional.
On Naval Warships the increased capability on a single platform has driven an increase in crew size and crew are still in general divided by competencies and functional departments.
The commercial shipping industry has halved its crew size over the last 20-30 yrs with increased focus on automation and crew becoming more multi-skilled.
Naval crewing policy has not changed in the same manner as the commercial shipping industry with the introduction of more automated equipment. Crew sizes have been maintained with vessel size and vessel capability has increased with the focus being on multi-functional platforms.
Taylor Bros has been involved in numerous installations and studies where modern crew habitability standards have been applied (Or attempted to be applied) to installations and the increased vessel capability has driven a crew increase. A compromise needs to be made and some clear direction from Navy would be appreciated.
The devil is often in the details but any crew increase has a flow on effect to other ships auxiliary systems, while any crew decrease will have the same flow on effect but in the reverse direction. Such an effect can have some major impacts on ship capability such as ship displacement, range and particularly endurance.
ENHANCING FUTURE SURFACE COMBATANTS THROUGH ADVANCED SHIP DESIGN DIGITAL TWINS
Leonie Wong, SIEMENS DI SW, Australia
Dr. Rodrigo Perez Fernández, SIEMENS DI SW, Spain
Marc Shipley, SIEMENS DI SW, UK
This paper explores the transformative potential of ship design digital twins in optimizing the performance, resilience, and operational capabilities of future surface combatants. Digital twins, advanced simulations mirroring real-time vessel behaviour, are poised to revolutionize naval engineering by providing unparalleled insights into the intricate dynamics of maritime operations.
By integrating cutting-edge technologies such as artificial intelligence, data analytics, and sensor networks, these digital twins offer a comprehensive understanding of a ship's structural integrity, propulsion systems, and onboard functionalities. This paper elucidates how leveraging ship design digital twins can empower naval architects and operators to enhance decision-making processes, streamline maintenance procedures, and bolster overall mission effectiveness. The study underscores the imperative role of digital twins in fostering innovation and adaptability within the naval domain, heralding a new era for future surface combatants.
Expanded Thought: A Lightly Crewed and Highly Automated Warship Design
Dr. Shelley Gallup, Naval Postgraduate School
The U.S. Navy and indeed allied partners face challenges in the South China Sea. There is a need to focus on design to “fit” operational realities in this region. The United States must deal with the “tyranny of distance,” and lacks the numbers and types of warships needed to face down a burgeoning threat, bent on creating a fait accompli that would be impossible to reverse, short of all out war. And allied nations of the region need to play a role. Solutions are possible in the near term, but U. S. Navy force design options are continually laser-focused mostly on full autonomy, or unmanned “drone” missile platforms. This is a challenge to naval and maritime thinkers, trying to consider how to get as much variety in action and reaction into contested maritime environments. Here we discuss operational art as it affects ship design to form alternatives to our Navy’s current force design acquisition paths. We look first to a naval force as a “system (deterrence) regulator,” and then consider needs for an evolutionary approach to distant future capabilities while managing the present near future. Finally, a highly developed lightly crewed but very formidable warship design (LMACC; Lightly Manned Automated Combat Capability) is presented that meets the needs of current and emerging competition in the South China Sea. Innovations that make this design concept possible are introduced, along with a generalized Concept of Operations.
Registration
Cancellations received in writing up to two weeks before the event takes place will be subject to administration charge of £200. Cancellations received after this time cannot be accepted and are subject to the full event fee. Delegates may be substituted; however, this must be sent in writing and confirmed with the RINA Events Team. It may be necessary for reasons beyond our control to alter the content and timing of the programme. In the unlikely event that RINA cancels the event for any reason, our liability is limited to the return of the registration fee.
Personal Data
Please note that personal data, such as name and company, will be collected and provided in the delegate list format to the event attendees. No contact details will be included in the delegate list. If you would like to not be included in the list for any reason, please inform the RINA Events Team at events@rina.org.uk
Filming/Photography
Please note that filming/photography will be taking place at this event for promotional and archival purposes. The photographs and recordings made are likely to appear on our website and social media. If you would prefer not to be photographed please let the Marketing team know at marketing@rina.org.uk.
Sponsorship Opportunities
RINA events provide the perfect opportunity for effective and highly targeted marketing. Sponsorship and exhibition opportunities exist for all of our conferences. For more information please click here.
If you have any questions regarding the conference, please get in touch with the RINA Events team at events@rina.org.uk
Continual Professional Development
Attendance at the RINA conferences and courses qualifies as Continuing Professional Development. On completion of the course a CPD certificate will be issued.
Registration
Please note:
Your membership number must be entered when choosing a membership rate, otherwise your order will be subject to cancellation.
Bookings are closed for this event.