ICCAS 2022
International Conference on Computer Applications in Shipbuilding
The 20th International Conference on Computer Applications in Shipbuilding (ICCAS), to be held in Yokohama, Japan. The conference will run 13-15 September 2022 , with visit to the National Maritime Research Institute (NMRI) on 16th September.
Continuing the noteworthy success of previous conferences, ICCAS offers unequalled opportunity for international delegates from the global shipbuilding and marine industry to see practical application of computing technologies across all aspects of design, production, and in-service operation of ships and marine structures.
ICCAS will include papers on all aspects of shipbuilding. Delegates can understand the implementation, success and benefits of applying computing technologies in the industry to improve methodologies, processes and productivity.
Topics
ICCAS encourages papers on all applications of computing and information technologies for use within the Shipbuilding, Marine, and Ship Operation related industries.
The primary topics for ICCAS conferences are typically:
- Evaluation, selection and implementation of a new system.
- Enhancement and/or improved use of existing computing and IT systems.
- Efficient use of data and information captured in Computing Systems.
- Research and development of a future applications of Computing Technologies the industry.
- Vendor development of system capabilities and/or functionality.
- A vision of the future potential use of Computing Technologies within the industry.
- Using Computing Technologies in a collaborative or multi-site environment.
- Procedures and practices implemented to maximise use and benefits of Computing Technologies.
- Improvements in productivity and/or performance due to the use of Computing Technologies.
- Success in applying advanced technologies (such as simulation, AR/VR, Engineering Analysis, Digital
- Manufacturing, Big Data, Digital Twin, Knowledge Systems, etc).
- Improvements in manufacturing quality/accuracy/productivity due to computing methodologies.
- Topics not listed above that are relevant to the industry, which are also acceptable.
ICCAS attracts topics from any stage of a ship lifecycle, from concept and early design, through detail design, planning and project management, manufacturing, production and assembly, build, and in-service operation.
Topics such as a supplier using computing technology to enhance equipment performance, a classification society that uses computing technologies to improve the quality and format of data for approval assessment, or a ship operator using computing technologies to optimise performance, are very welcome.
ICCAS particularly welcomes papers discussing the practical application of the topic in production, or proven during field trials.
Abstracts
Emergent Simulation Techniques in the Development of the Quiescent Period Prediction (QPP) Flight Deck Motion Forecasting Tool
B Ferrier, Hoffman Engineering
Ministry of Defence / University of Exeter’s Quiescent Period Prediction (QPP) purpose is to provide ship motion conditions and motion predictions with sufficient forecasted time (over a minute) to launch, recover and complete other motion sensitive tasks regardless of the seaway. The specific objectives are: (i) is to both give the operator guidance on the optimum ship’s heading and speed to initiate launch/recovery vehicular activity and (ii) to predict the quietest period of flight deck motion (for safest recovery) over timescales of typically 60 to 120 seconds ahead. to expand ship UAS operating deck limits to approximately Sea State +6.
This article describes the simulation techniques used in the development of the QPP system tool. If is based and operates within a High-Level Architecture (HLA) application allowing plug and play of various measurement federates such as a Wave Radar system. It is used to map remote sea surfaces several hundred meters in advance of the ship to enable the computation of predictions of the future wave forces acting on the virtual vessel. Such technologies have “look ahead” time horizons measured in minutes and are typically designed to identify “Quiescent Periods”. These are “the safest recovery periods” for launch and recovery and make it possible to safely execute an operation when the “mean” prevailing conditions exceed the traditionally considered safe limits.
This article describes Proof-of-concept simulation test procedures, timely seaway mapping and ship motion computed characteristics specifically designed to complete a motion sensitive task like UAS launch and recovery.
Plan, Do, Check, Act: Enabling the Deming Cycle for Ship Production
C Zerbst, Prostep
Managing shipyards production poses a permanent challenge. Preparing actions to be executed for example in 6 months requires a lot of guesswork, as the exact product structure has not been designed yet. The information basis improves over time, but even planning the next week is quite an undertaking. The large-scale product, distributed production sites, late changes requested by customers, production failures, or missing deliveries are only a few obstacles to name. These make it difficult to acquire a full understanding of the situation and plan optimal steps with a reasonable effort and in due time.
A joint research project called ProProS run by Lürssen Yard, RWTH Aachen, and PROSTEP seek to improve this situation. The goal is to implement a real-time enabled planning system specifically for ship production. To achieve this goal, we want to provide enough information about the todays situation as well as insight into possible outcomes of current planning. This allows production planners to run a full Deming cycle on a daily basis. Doing so requires tight integration with existing design systems for assembly planning as well as receiving status feedback from production. Insight collected on the currently performed production steps is also feeding a machine learning component. Its result is used to achieve better estimates on the production resources needed for example in six months.
A route planning method for coastal navigation of small ships
D Jeong, Seoul National University
The route planning method has been proposed and developed in various fields such as robotics, navigation for vehicles, computer games, etc. A route planning for ship navigation should consider multiple purposes for finding the route depending on the types of ships. Especially, small ships are mostly operated near the coastal area and used for personal purposes. From this point of view, the resolution of the map for route planning should be high to avoid obstacles in the coastal area for small ships. In addition, various objects on the sea should be presented on the map efficiently. In this study, the route planning method for small ships such as yachts and ferries was proposed. For this, the quadtree grid was selected as the data structure for the high-resolution map instead of the uniform grid because the quadtree grid can represent the specific region in more detail by dividing only the desired part of the map. For personal use, routes for navigation should be provided within a short time. Therefore, the computational speed of route planning should be fast. HPA* (Hierarchical Pathfinding A*) was applied for faster route planning. And S-57 prescribed by IHO (International Hydrographic Organization) has various regulations for coastal navigation. Therefore, various methods were additionally considered to satisfy the regulations. The proposed method was applied for route planning in coastal areas in the Republic of Korea. From the results, the efficiency of the proposed method was evaluated compared with the existing route planning algorithm.
Coupling a high fidelity near surface effects model into PARAMARINE S4
P Crossland and C Forrest, QinetiQ Ltd
When a submarine is operating at depths typical of those required when using the periscope, snorting during the period of recharging the batteries or, in the some cases, at slow to zero speed whilst hovering, the submarine can experience complex oscillatory motion due to higher order sea loads. The second order vertical plane loads can manifest themselves as a mean and time varying suction force effectively causing the submarine to be drawn to the surface risking broaching and increasing the possibility of detection. Current methodologies for modelling near surface effects tend to utilize coefficient-based methods to represent the first and second order wave forces on a submarine body. These empirical methods may be suitable for some applications but are not able to capture all the effects of the submarine operating close to the free surface. As the body approaches the free surface, the flow field around the submarine is modified by the gravitational wave effects, changing the pressure distribution across the body and hence the forces and moments. This change in force is dependent upon the shape of the body and the environment and, therefore, it is impractical that a coefficients based approach could cover all these scenarios to any great level of fidelity.
This paper presents a potential flow method for quantifying the hydrodynamic loads on a fully appended submarine when in proximity and under the influence of surface waves. The paper presents some validation of the method and describes its integration with the PARAMARINE S4 submarine manoeuvring software.
Automatic Data Extraction and Unfolding for Ship Hull Plates on CATIA
Y Hu, Wuhan University of Technology
In view of the current low efficiency of ship production and the shortcomings of various software in the unfolding of ship hull plates, in this study, a method that automatic data extraction and unfolding of ship hull plates is proposed. This method has carried out by the add-on development of the Component Application Architecture (CAA) on CATIA 3DEXPERIENCE platform (3DE platform). The sequence of the method is as the following: Firstly, the model is switched into the editable mode. Then, the file tree is traversed for judging the type of parts and identifying the geometric features, and the intersection lines between surfaces and the structural lines are generated. Thirdly, the neutral layer of parts are extracted and the process information (e.g. margin, compensation and bevel) are added. Finally, the information extracted are integrated into an exchange file for unfolding or processing. Different methods are proposed for flat plate, curved plate and combined plate. As for the double-curved hull plate which cannot be directly unfolded, an approximate unfolding method of dividing the plate into strips and small triangles and then splicing them together is proposed according to the forming method of plate. The test result shows that this method can reliably extract the plate parts and unfold the curved plate.
Dynamic optimization of port operations onboard a typical Ro-Ro vessel, aided by a smart decision support system
C S Uppal, Cochin University of Technology
The speed of a Ro-RO vessel’s operation is governed by the time it spends on port in order to undergo various operation like loading & unloading. The increase in vessel size and cargo demand has led to an inherent need of better planning which as of now is very chaotic and un-standardized, hence rendering simple port operations, not only a havoc but requiring a large amount of unnecessary ballast. This has led to an increased consumption of time while leaving a bad impact on the environment. Not only thus the port operations have become more labor intensive but also require sensitive calculations at various stages, thus increasing the probability of accidents onboard and on port.
The paper proposes the use of mathematically modeled simulation as the basis of decision-making, aiding various port operations associated with Ro-Ro vessels, to achieve higher performance, reduced time-consumption & decreased environmental impact. Furthermore, it provides us with various calculation intensive parameters related to the vessel’s cargo which would otherwise be very laborious and time consuming to calculate.
The study approaches the problem at hand in a variable – specific program-oriented simulation taking a general Ro-RO vessel design as a template. This makes the application of the developed mathematical model universal & flexible over a wide range of Ro-Ro & Ro-pax vessels. The automation process hence developed is not specific to any particular Ro-RO vessel but is rather concentrated at optimizing the operation being performed.
The main objective of this study is to establish a load planning model for a Ro-Ro vessel, optimizing trim, heel and keeping a close & strict watch on structural integrity of the vessel leading to a reduction of time & pollution caused by the operation.
Automated Generation and Low Effort Authoring of Commissioning Content in the Maritime Industry
A Elzalabany, Technical University of Hamburg
Commissioning in the maritime industry is a long crucial phase in which all essential components in the ship are tested for faults and defects before a final acceptance form is signed by the client. Due to the variety of components in a ship, and the complex hierarchical structure of such components, it is typical to have thousands of tests that should be performed throughout the commissioning phase. For every new ship, content creators initially spend hours preparing the commissioning tests by reading technical documents, extracting relevant information, and applying the gathered knowledge to the unique equipment configuration in the ship. This leads to high preparation effort and planning mistakes (e.g. unconsidered dependencies), and as a result, commissioning and the ship building process as a whole may be delayed.
This paper lays the foundation for automating the process of authoring commissioning content for maritime productions. The paper presents a digital modelling approach for maritime components, which facilitates the development of commissioning-specialized software. The model shown in this paper takes textual and geometrical information of a ship component as input data, and produces generalized commissioning templates that can be used to automatically generate commissioning tests. Moreover, the paper discusses the potential of reusing commissioning templates in order to reduce the initial manual effort for new ships.
Digital Enterprise Platform Enables Efficient Shipbuilding
J Bitomsky, Prostep
Building commercial or naval vessels successfully is a highly complex process. Thus, sufficient project management faces multiple challenges: the integration of the various domains and partners involved, maturity management at project milestones as well as efficient change management due to requirement changes during the project. Without a proper handling of these challenges project targets (quality, cost and time) will not be achieved and are leading to an increased project risk. In that manner sufficient project management is a key enabler for shipbuilding.
During the recent years, an increasing trend of merging shipyards and existing shipyard groups to even bigger shipyard groups has been recognized. The reduction of costs by enabling synergies is one of the main drivers for shipyards. By an alignment of processes, a significant reduction of costs can be achieved. However, any operational optimization requires seamless IT integration to ensure information access throughout the entire shipbuilding and distribution processes.
To meet these requirements a digital enterprise platform supporting the entire process from initial design to operations from information as well as process perspective is needed. Building the digital ship model requires information flow as well as traceability across a variety of authoring and management systems. For this purpose, PROSTEP developed OpenPDM SHIP to enable integration as a product for the marine and offshore industries.
The present paper provides insights into real shipyard requirements from around the globe on IT integration to cope with the challenges above. Further, our experiences on technical solutions for seamless integration are provided.
Obstacle Detection and Tracking of Unmanned Surface Vehicles Using Multi-view Images in Marine Environment
J Park, Seoul National University
The unmanned surface vehicle (USV) is recently getting more attention with the development of autonomous navigation technology. The USV operates for various purposes, such as marine reconnaissance and survey, and it can operate as a group according to specific scenarios. In this study, a method of obstacle detection and tracking of USVs using multi-view images in marine environment was proposed. We assumed each USV detected marine obstacles by the camera mounted on itself and tracked the position and speed of the obstacles. For this, the YOLO algorithm, which is one of the real-time object detection algorithms based on CNN (Convolutional Neural Network), was adopted after fine tuning. Subsequently, the relative position of the detected obstacle was estimated through the position estimation algorithm of a monocular camera. Then, the position, speed, and course of each obstacle were tracked using the extended Kalman filter. Finally, the accuracy of the tracking results was improved through the data fusion of the tracked data from multiple USVs. The proposed method was validated through the actual field test using multiple USVs. As a result, it was confirmed that the proposed method could be useful in detecting and traking the obstacles in maritime environment.
Digital Platform Enabling Robotic Survey, Repair & Agile Manufacturing of Ships and Watercraft
F Santo, Lancaster University
In this work we developed a digital platform that has the potential to connect the European shipbuilding and ship maintenance supply chain & value chain. The platform provides digital design (e.g. Computer Aided Drawing) and simulation functionalities (e.g. Digital Twin) that allows users to design modular ship units and components for fabrication, repairs and maintenance. The platform also provides digital connectivity tool, which facilitates communication and collaboration between the European ship operators, the European Shipbuilding community and maintenance stakeholders, though the secure industry 4.0 information sharing support. The digital tool promotes collaborative production engineering approach. As a part of this work, we are also developing underwater Friction Stir Welding (FSW) robot and Remotely Operated Vehicle (ROV) in order to survey, repair and maintain part of the ship submerged in water, while it’s under operation. The platform establishes connection with the FSW robot and ROV hardware through the Websocket API. The connection provides two advantages. Firstly, the connection allows real-time data (i.e. numeric and video) from the hardware’s sensors to be feedback to the platform. The platforms data visualisation functionality provides users a real-time representation of these data. The data is also stored in the platforms database for post-processing and future training. Secondly, the connection facilitates the control of both the hardware through an intermediary computer. The digital platform in combination with the robotic solution enables rapid survey, repair and maintenance of ships under water and enhances the competitiveness of the European shipbuilding and maintenance sector in the global market.
Zero Infrastructure Geolocation Of Nearby First Responders On Ro-Ro Vessels
D Zeinalipour, University of Cyprus
The early suppression of fires on ro-ro vessels requires rapid fire identification as a fire of medium growth exponentially reaches 50kW after only 1 minute. Fire patrol members (e.g., able seamen) are asked to act as first responders in such fire incident cases. They do however lack the necessary digital technology for immediate localization, verification and coordination with the bridge and other first responders. Indoor localization requires dense referencing systems (such as Wi-Fi, UWB, Bluetooth antennas), but these technologies require expensive installations and maintenance. Also, Satellite-based localization is obstructed by the bulky steel structures of vessels, so this does not work either. Within the LASH FIRE project, an H2020 funded project (Grant Agreement #814975) in which this publication is framed, research has been carried out to develop a ground-breaking localization technology that requires zero infrastructure using computer vision on commodity smartphone devices attached to the gear of first responders. The developed solution comprises of two steps: (i) Training, where vessel owners supply video recordings that are processed on a deep learning data centre to produce an accurate mapping of non-movable vessel objects to the coordinates of a vessel; and (ii) Localization, where a designated mobile application localizes first responders on a digital map, shares their location, emergency messages and heat scanning images with nearby first responders and the bridge, using a sparse Wi-Fi or Mobile communication network. Our proposed technology streamlines the lengthy fire verification, coordination, and reaction process in the early stages of a fire, improving fire safety.
A Method of Variable Recognition and Connection for Reviewing Ship Regulations
M Kong, Seoul National University
The shipbuilding company requests the ship classifications to inspect a ship to obtain permission to construct or operate. The ship classifications review whether the ship complies with all design regulations by referring to the relevant regulations. Owing to the characteristics of the shipbuilding industry, the relevant design regulations are detailed, interrelated, and complex. Accordingly, reviewing all relevant regulations is difficult for even professional reviewers. Therefore, this study proposed a method of automatically indexing regulations and recognizing the variables to visualize the relationship between each variable and the indexed position. For this, it is necessary to accurately extract and process the components in the regulations distributed in portable document format (PDF). Firstly, we extracted characters, texts, equations, and the table of contents in the regulations using the library for the PDF extraction. Using extracted components, we matched the extracted table of contents and text components with similar components using the Levenshtein-distance algorithm. In addition, the regulations were indexed according to the table of contents. Secondly, the subscript and superscript were separated to recognize variables using the positional relationship of the extracted characters. Finally, the indexed position of each variable and the connection relationship between each variable were visualized. The method proposed in this study was applied to review the common structural rules (CSR), and its effectiveness was evaluated by showing a high rate of variable recognition and indexing accuracy.
Application of mixed reality technology to ship manufacturing process
Y Mimori, Mitsubishi Shipbuilding Co., Ltd.
In recent years, the evolution of so-called XR technologies and devices such as virtual reality (VR), augmented reality (AR), and mixed reality (MR) has been remarkable, and has spread widely, especially in the game and amusement industries. XR technology is also used in some products in the manufacturing industry. Widespread use of XR technology in design and production is one way to support Japan’s manufacturing industry, which is expected to experience labor shortages due to a shrinking population. In particular, AR/MR is an epoch-making technology that merges the real world with the virtual world, allowing users to experience the work that will be completed in some days or months ahead, and to perform more efficient work by displaying construction instructions and design information on actual workpiece.
Since the 2000s, the Mitsubishi Shipbuilding Division has been promoting the digitalization of shipyards using the 3D viewer (HullViewer/FitViewer) developed in-house. The 3D Viewer has a dedicated function to support the shipbuilding design and manufacturing process and is used in many other shipyards in Japan.
As the next step, we are working to further improve productivity and quality by introducing MR technology to our production sites that allows workers to experience a more realistic virtual space.
This paper reports the progress of development and application of MR system for shipbuilding based on Hololens2 of Microsoft.
Sustainable Ship design with Modular Shipbuilding approach
R Audoire, Dassault Systemes
The present paper presents the approach used for the European project called NAVAIS (New Advanced Value Added Innovation in Shipbuilding) to develop a ship design and construction approach that minimizes the impact on the environment.
The approach includes a specific attention to Underwater Noises, Vibration Noises, and Propulsion Reduction thanks to simulation technics and solutions.
The approach also focusses on modular design, to foster re-use of standard modules, and digital collaboration platform technics between all actors.
The overall process relies on Model Based System Engineering (MBSE), and allows to move from an Engineering To Order (ETO) conventional ship design method, to a Configuration To Order (CTO) method.
Another benefit of this new approach is the ability for the class society to pre-approve the various pre-designed systems modules in advance, thus saving time during the final approval process.
The paper presents the research work that has been achieved on that topic so far, and will leverage demos and videos that have been produced by the members of the project.
A position estimation system for indoor workshops making use of maximum likelihood estimation in Weibull distribution model of wireless LAN
H Kimura, Kyushu University
In the shipyard, it is required to obtain the position of people and goods in order to manage people, objects, improve work placement, and secure workers’ safety. Although the mainstream of location estimation is GPS, it can not be used for position detection at indoor workshops. Meanwhile, the infrastructure of the wireless LAN has been in place in recent factories, and if these can be used for position detection, the installation cost of facilities for position detection can be reduced. In this research, we investigate a location estimation method based on a certain statistical algorithm using radio field intensity distribution map of unspecified number of wireless LANs without specifying the access point installation site of wireless LAN, and verify the position estimation accuracy in several indoor workshops.
Autonomous Mobile Robots introduction in shipyards’ manufacturing process
C Dentesano, Fincanteri
In the context of an exponential growth of digitalization in the naval production process, the introduction of emerging technologies becomes a key point for the future competitiveness of companies. As a matter of fact, it is fundamental to optimize the process as a whole, exploiting newest solutions to improve production tracking, quality control and time-saving.
Specifically, autonomous mobile robot technologies (AMR) are becoming increasingly relevant in recent years, thanks to the advances in the scientific community and to the growing number of market options.
In this scenario, it was decided to use AMRs to face different problems in the shipyard, such as autonomous inspections and material transport, in order to provide our employees with a concrete and automated support during the tasks of every day. As a result, our work led to a cloud ecosystem where our workers have the possibility to assign specific tasks to robots, like setting up real stocktaking missions or making requests for missing material, while putting their effort in more worthwhile activities. Humans and different kinds of mobile robots can operate within the same environment without hindering each other, and the autonomous mode can be easily turned into a controlled one.
In this paper, we are going to present the research and development journey which took us to the deployment of a concrete solution for improving both efficiency and quality of our shipyards, which fits perfectly into the framework of digital innovation of our company.
Virtual reality beyond design reviews in shipbuilding : the need for industry-tailored immersive data interaction.
N Fourrier, Segula Technologies
In the context of ship outfitting, and more generally in shipbuilding, the potential of virtual reality (VR) as a visualization tool has been widely demonstrated in the literature. For example, its effective use as a design review tool has been proven in many fields. While many conditions must be met for VR to be widely adopted in the shipbuilding industry context, it primarily must be seamlessly integrated into current workflows. To do so, the shipbuilding industry will likely first need to tame its data. Indeed, the use of efficient knowledge and data-bases, such as the building information models (BIM) used in architecture, accessible throughout the product lifecycle, could significantly improve our ability to integrate VR in present-day processes. However, text input techniques in VR are cumbersome and inefficient and do not allow for an easy exploration and manipulation of such knowledge bases. There is a need for novel VR input techniques, designed with industrial use in mind, that are efficient and easy-to-learn. We argue that such new techniques combined with easily consumable data would allow VR to be used as a manipulation tool for collaborative and interactive design purposes such as ship outfitting. In that respect, we propose a new VR text-entry technique based on handwriting recognition (HWR). A comparative user study, yet to be carried out, will confirm whether or not HWR could rival current techniques in terms of input speed, precision and cognitive load without a need for training.
Streamlining the ship structural optimization process by using an early 3D product model
T Masui, NAPA Japan
Optimization of ship structure has been a target for ship designers ever since the beginning of the modern shipbuilding industries. Total optimization is a challenging task because of the many dependencies, starting from the local production facilities up to geopolitics and world economy. At the same time, class societies’ rules and regulations are continuously evolving and guiding the shipbuilders around the world in their use of more advanced methods and tools, which will further facilitate the optimization of structures against the latest knowledge. The new rules and dedicated software for utilizing these will bring new challenges for the ship design process, which is getting more complex, with iteration processes taking considerably longer calendar time. This may affect ship builders’ competitiveness in launching new products and limit the use of the full range of all the new technological knowledge and possibilities for structural optimization. This paper presents some results of a project, in which the optimization process is built inside one technology platform. This platform combines the necessary modelling work, FEM based rule check and further weight and other calculations in one automated and streamlined process. This will have a tremendous effect on the throughput time of iteration cycles. The paper will present the process and technologies used for integrating the different components to the common design platform. It will also show some results achieved in a commercial cargo ship design.
Vehicle Hot Spot Detector And Dangerous Goods Detector To Fire Ignition Prevention In Ro-Ro Ships
Á Marrero, CENIT Research Group of CIMNE
Statistics show that 90% of ro-pax ship fires are initiated in the carried cargo (vehicles and cargo units), which can be everything from brand new to poorly maintained, rebuilt or unsafe. Nowadays, all cargo (except dangerous goods) is loaded without consideration to the hazards they pose, opening the door to improvements from the fire prevention point of view by means of a custom and objective management of the units based on the potential hazards they involve. Thus, the need of providing innovative mechanisms supporting the screening stage, arise. Within the LASH FIRE project, an H2020 funded project (Grant Agreement #814975) in which this publication is framed, research has been carried out addressing automatic identification of different types of cargo during the stowage in order to provide added-value about cargo status. The technical approach presented here takes the systems currently used in parking lots, tunnels, tolls or logistics as starting point but applied to the maritime environment. Specifically, both Vehicle Hot Spot Detector (VHD) and Vehicle Dangerous Goods Detector (VDG) have been modified and extended with developments that now consider usual loading units in the above-mentioned type of ships. Also, a refactoring has been performed aiming at adapting the system to the environmental conditions in which it must work.The VHD and VDG systems delivers the exact length and volume of the vehicles and indicate the licence-/ dangerous good plate. The dates are used in cloud based new online stowage tools for loading optimization. This enables more safety on board.
Stowage Planning Tool Supporting Fire Risk Management: A New Way For Cargo Distribution
F Rodero, CENIT Research Group of CIMNE
Feeding from the outcomes obtained after performing a risk analysis based on historical data to prevent cargo ignition on Ro-Ro, Ro-Pax and Car-Carrier ships, this paper describes the foundation for the development of a tool supporting fire risk management during the cargo distribution stage of the stowage. In this process, cargo other than dangerous goods are loaded without consideration to the hazards they may involve, leaving room for improvements from the ignition prevention perspective. The boundary conditions of the problem being addressed are defined by the scope of LASH FIRE, an H2020 funded project (Grant Agreement #814975) in which this publication is framed. An approach to both design and specification is presented, aiming to manage all the optimization actions needed to obtain the best placement of cargo units, understanding best as the combination that minimizes the overall risk of fire. This way, a detailed description of inputs being used and constraints taken into consideration together with an explanation about how the tool can interact with existing software of operators are included. Details on the implementation are also covered, showing how the algorithm can play a key role during decision-making to get safer voyages. Finally, conclusions based on the outputs obtained after testing the tool in generic representatives for the abovementioned ship types can be found in this paper.
Smart Digital Shipyards with Model-Based Manufacturing
O Chouche, Dassalt Systemes SE,
Smart Digital Shipyards covers the entire life cycle of shipbuilding. From requirements, to Design and Engineering, to Digital Manufacturing, to Manufacturing execution. Model-Based Manufacturing will ensure all the information required for shipbuilding will be available in a unified model within a collaborative platform. This will seamlessly support all the manufacturing processes without having to go through non-value add activities.
Until today, many shipbuilders still use disjointed primitive tools to manage sophisticated processes. Tools such as Excel spreadsheets as well as lists and 2D drawings printed on paper. Production teams manage warehouses with tools developed over a decade ago. Shipbuilders also address production issues inefficiently – they often rack up a significant amount of additional work hours, going beyond the agreed project timeline and incurring massive extra costs. In the past, this approach may have been acceptable, but today’s environment is less forgiving.
This paper will introduce the major transformation undergoing at some leading shipyards, by replacing the traditional document based processes for a model-based manufacturing approach leveraging ship virtual twins from design to production, achieving a strategic move towards ‘Smart Digital Shipyards’.
The presentation is highlighting the related business changes and platform technologies involved in the model-based shipbuilding transformation, illustrated by examples of a successful implementation at a leading Chinese shipyard witnessing major benefits of time, cost and quality on their first projects fully executed with a model-based strategy.
A major component of smart digital shipyards is the connectivity of major manufacturing equipment that are essential to the manufacturing execution process. Equipment such as pre-treatment lines, panel lines, and assembly lines. Also, the integration of Internet of Things (IoT) to evolve shipyards for the modern era. Sensors and monitoring systems can communicate huge quantities of data that will enhance the capacity for predicting and greatly reducing operational downtime. A connected shipyard can improve planning activities and reduce maintenance costs through predictive maintenance.
At the core of digital shipyards is the adoption of model based enterprise approach. This approach provides the ability for the information to flow seamlessly from one process to the next. No need for translation or migration of data between different processes. It is one single model that supports all the processes of the entire lifecycle. Specifically, during each process, the model is enriched with additional information which is then used by other enterprise users and downstream processes.
The 3DEXPERIENCE platform provides all the components needed for an integrated model based enterprise solution for requirement capture, engineering, manufacturing, maintenance, and operations.
A Mobile Application to Assess the Stability of Small Fishing Boats
A Grech La Rosa, University College London
Indonesia is one of the top three countries in the world for fisher fatalities and this is due to a lack of stability monitoring, poor vessel design and the fishers’ poor safety culture. Safety through using technology, in particular specifying stability awareness has been identified as a key aspect to prevent capsize and sinking.
Despite the low technology uptake by Indonesian fishers, they are known to make extensive use of smart mobile phones as a primary form of communication. These devices are equipped with an array of sensors that can be used by different mobile applications.
This paper proposes the use of a mobile application to aid Indonesian fishers assess the stability of their vessel by using results from a roll decay test or real time roll motion data monitored when operating at sea.
For the roll decay test, the mobile application uses the onboard gyroscope to record the roll angle time series to quantify the roll period. An offline calculation is then carried out to approximate the vessel’s metacentric height, that is visually interpreted by a traffic light system. This gives the fishermen an indication of whether the vessel is stable or not. Should the boat be unstable, additional guidance is provided to improve the vessel’s stability.
The real time monitoring system alerts the fishers when the thresholds are exceeded, to make them aware of the increased risk. This is increasingly important as the vessel loads fish and encounters waves.
A case study demonstrating the functionality of the application will be provided using full scale data.
Development of Shipping Market Forecasting System Using Vessel Movement Data and its Practical Application
Y Wada, Hiroshima University
Shipping is an industry in which the changes in freight rate has been extremely drastic. Therefore, it is important for shipping companyto develop a forecasting method of freight rate. In recent years, big data and deep learning methods have been developing rapidly, and these are applied in a variety of fields. In shipping industry,the details on movement data of each ships can be available by development of automatic identification system (AIS). Therefore, it is expected to define a practical forecasting model combing AIS data and statistical data, and using deep learning method. In our previous study, we have proposed a method to develop forecasting model for freight rate by conbing AIS data and statistical data using deep learning. As a result, we have confirmed that highly accurate model can be develoepd using these data and the method. However, there were some issues as follows:
・The range of applicability of the forecasting model is not clear.
・The accuracy of forecasting model is not sufficiently understood compared to the predictions of experts.
・It has not been possible to verify whether the forecasting model can be used in practice.
Based on the above issues, this study analyzes the causes of deterioration in forecast accuracy from the perspective of internal factors of the forecasting model. In addition, we will develop a prediction system and veryfy the applicability in practice. Moreover, we confirm the superiority of forecasting model against experts prediction using developed system.
Development of a Pipe Fabrication Process Determination System Using Graph Database and Process Simulation
Y Mihara, Yokohama National University
As the importance of piping in shipbuilding increases, streamlining pipe fabrication processes has become one of the most important issues. However, since pipe fabrication processes are very complicated, it has not been adequately digitized and modeled.
This paper proposed a system to automatically determine the pipe fabrication process considering the design of the target pipe and various information in a factory. In the developed system, tasks are generated using the information of the parts and these relationships registered in a graph database. This system also generates all conceivable fabrication processes by allocating workplaces to each extracted task.
Optimal fabrication process is selected by executing the production simulation using the information of target factory, the information of each fabrication process and target product generated on the graph database.
The developed system is applied to three virtual pipe fabrication factory which has the same mission of producing a target pipe. Results show that the optimal process determined by the developed system is dependent on the configuration of the pipe factory and the capability of facilities and workers.
In addition, the developed system is applied to a real pipe fabrication factory. We can confirm that the process determined by the developed system is reasonable compared to the currently adopted process.
Interceptor Effects on a 3D Rectangular Plates in a Calm Water by Using Computational Fluid Dynamics
A M F Putra, Osaka University
Interceptor is an additional device designed to improve boat efficiency by altering its running attitude. Interceptors are recently used for trim control and steering, in order to reduce uneven motions of the boats, especially in the early stages of the trip. Controlling trim during the trip can result in a significant reduction in water resistance, resulting in improved efficiencies. This paper focused on the hydrodynamics effects on resistance and trim of 3D rectangular plate in addition of interceptors in calm water by using Computational Fluid Dynamics (CFD). Various configuration of blade deployment, by depth and angle of attack (AoA), were used in the simulations. Investigation has been carried out by using Open source CFD code, OpenFoam. The results of this study generally meet a good agreement with most of previous works related to interceptor’s study. This study found that AoA employment at the interceptor with typical blade depth height shows better lift to drag ratio in comparison with interceptor without AoA employment. Moreover, those configurations also produced better trim angle reduction which resulting better running attitude. This study also shows that the efficiency of the interceptor is related to the boundary layer thickness.
MAKING 3D MODEL-BASED APPROVAL A REALITY
T Masui, NAPA Japan
In recent years, various classification societies and shipbuilders have conducted R&D activities on the use of 3D models created during the design phase for approval (so-called 3D Model-Based Approval, hereafter “3DMBA”). 3DMBA is an attractive concept that could bring digital transformation to the ship design process, but it also poses significant practical challenges. In particular, there is an issue about the division of design work and information in structural design, which requires the use of different software applications for different tasks such as 3D modeling, rule calculation, direct strength calculation, and 2D drawing. This causes a situation whereby each time a design change happens, it is necessary to modify the data in each software, resulting in frequent duplication of work. This is also an error-prone process, because of possible discrepancies between various types of information in each software. The introduction of 3DMBA under such circumstances would further increase the workload of shipyards, as they would have to repeat this duplication of work on each software application to complete a precise 3D model. The authors have been conducting a project in order to realize an efficient 3DMBA process, and they concluded at ICCAS2019 that the key to achieving 3DMBA is to integrate the engineering process for rule and direct strength calculations into 3D CAD, and to implement viewer functions for efficient plan approval in order to enable shipyards to easily create 3D approval models. This paper presents the latest achievements and future prospects of the project
An expanded application of Basic Ship-Planning Support System using Big Data in Maritime Logistics for Panamax and Capesize Dry Bulk Carriers
D A F Muzhoffar, Hiroshima University
The fluctuations in the global industrial cargoes require continuous ship advancement. Meanwhile, digitized shipping generates big data that opens a possibility to understand the actual and prospective circumstances. Thus, we have developed a basic ship-planning support system utilizing big data in maritime logistics. Prior studies enhanced a ship allocation algorithm that can consider the shipping cost (COST) and greenhouse gas (GHG) features. However, the previously built system was applied specifically for Capesize dry bulk carrier operating in the time-charter contract. This study presents an expansion of our system applicability to cover the target ship of Panamax and Capesize dry bulk carrier. We newly develop the cargo movement model to accommodate monthly cargo movement for those target ship. Moreover, we reinforce the ship allocation algorithm to take into account the target ship typical shipping scheme; voyage-charter contract. Therefore, the system enables fleet composition optimization at the operation-level by considering the COST and GHG, which operate in the manner of both time-charter and voyage-charter contracts. Finally, the ships in demand at various scopes can be observed depending on the determined simulation scenarios, such as all ship replacement while preserving existing fleet composition, an optimization of fleet allocation using only the existing ships, and an optimization of fleet allocation with the new ships presence.
Voyage optimization with wind propulsion
V Paakkari, Norsepower
The recent years have increased the demand for reducing the environmental footprint of shipping. This applies both to ship’s technical aspects, it’s overall energy efficiency but also operational aspects, how the ship’s full potential is used the most effectively. These developments, together with increasing fuel prices have created new interest in use of wind propulsion in shipping. Wind propulsion has been proven to produce significant fuel savings on commercial vessels. The typical savings potential of wind propulsion on conventional cargo ships is 5-25%. On the other hand, voyage optimization and weather routing has been shown to produce similarly large fuel savings in the order of 15%. Wind is an intermittent energy source, and it often occurs together with waves, making ships installed with wind propulsion especially interesting from weather routing point of view. This means that a holistic approach is needed when conducting weather routing for ships with wind propulsion. Using detailed simulations, this paper studies how the fuel savings potential of wind propulsion can be further improved by coupling it with state-of-the-art voyage optimization software. Via case study examples, it is shown that the savings potential of wind propulsion can be more than doubled by using voyage optimization. The paper also discusses how historical weather data, together with voyage simulation can be used to inform ship design. An example is shown where ships operational profile was kept with reduced main engine capacity once the ship was equipped with wind propulsion.
Information management in shipbuilding projects – uninterrupted information flow from 3D design to production data.
L Seppälä, Cadmatic
Managing the information flow between engineering, design, and production stages using a flexible platform approach with open data integration becomes mainstream in modern shipyards. An intuitive interface in the 3D dashboard and connection to AR/VR opens new possibilities for practical applications of the latest technologies and the next level of digitalization in shipbuilding. Digital technologies development and adaptation in shipyards often exhibit a gap due to a lack of alignment between tools’ possibilities and settled shipbuilding practice in a particular shipyard. Eliminating this gap ensures full-scale exploitation and benefit from digital technologies. Data quality, consistency, interconnectivity, and the maximized automation of data handling throughout the entire ship design and shipbuilding process are critical factors in unlocking greater efficiency, increasing productivity, and boosting the profitability of the shipbuilding industry as a whole. The paper presents main use scenarios and analysis of shipyard processes concerning technological tools, using CADMATIC information management solution and its use at shipyards as an example.
A Model-Based Decision Support Framework for Maritime Industry: Case Study of Alternative Fuels Deployment
K Hiekata, The University of Tokyo
Due to the complexity of the maritime industry and the uncertainty of technological development and organizational changes, decision makings for new technology adoptions and changes in policies for decarbonization and automation are very difficult.
We propose a framework to solve this problem and demonstrate it on the decision-making problem of policy design on alternative fuels for decarbonization. Specifically, we will work on the following. 1. Development of a simulation model that can reproduce the complex behaviors of maritime industry. The simulation model uses future scenarios consisted of demand, service speed of each ship, fuel prices and legislations such as carbon tax as input, then projects the revenues and carbon dioxide emissions for each year. Shipping companies are modeled as multi agents. The simulation can quantitatively evaluate the legislations. 2. Proposal of a workshop environment for a team that can deepen the understanding of the behavior of the entire maritime industry as a system by interactively using the developed simulation model. A team of three or four members uses the simulation models and investigate the detailed results of the simulation. The software for the simulation has user interface to evaluate different legislations or market configurations in an interactive manner. 3. We proposed the concept of the framework and developed a prototype system for a case study of alternative fuels.
Development of CAD based stability calculation software for Pure-Loss of Stability and Parametric Rolling Failure Mode of 2nd Generation Intact Stability Criteria
J Park, Korean Register
Although the IMO mandates IS Code Part A to build and operate ships, ship safety is not guaranteed due to the problem of dynamic stability. So, IMO prepared the second-generation stability standard with five modes. However, since the software supporting the second-generation stability calculation is insufficient, CAD-based stability calculation SW that supports the second-generation stability calculation was developed. And in this paper, we calculated the change in resilience by waves, and calculated the restoration performance in Pure-Loss of Stability and Parametric Rolling Failure Mode.
IoS-OP: Initiatives for ship operation data collection, distribution, and utilization
Y Ikeda, ShipDC
Internet of Ships Open Platform (IoS-OP), launched in 2018, is the common platform to collect, distribute, and utilize the operation data of ships to enable shipbuilders, manufacturers, and other stakeholders to share the data without infringing the interest of data providers expected to be shipping companies. The initiative has aimed to realize the big data infrastructure for ship operation beyond individual corporates and accelerate the development of data-driven solutions.
IoS-OP consists of the data center service and the common rules for data distribution agreed among the industry. The data providers are able to decide the extent to distribute their data, and the exchange process with data users has been standardized and streamlined to minimize the related cost and burden of stakeholders. The membership association called IoS-OP has been established to ensure the fair, reliable, and independent management of IoS-OP, and it has overseen and promoted various activities.
As of the end of 2021, 54 organizations participate in the consortium, and the platform stores operation data of more than 1,000 ships available for distribution.
The paper describes the framework of IoS-OP, including API for data exchange as well as the common rules, and the current and projected use cases on IoS-OP to demonstrate how the data that transcends corporate boundaries bring about benefit to the industry.
A study of process simulation based on a multi-agent system for shipbuilding
T Taniguchi, National Institute of Maritime, Port and Aviation Technology, National Maritime Research Institute
This study proposes a process simulation based on the multi-agent system. Also, the utilization of the simulator is examined for the digital transformation of shipbuilding. Simulation techniques are conventional methods for man-hour estimation, schedule optimization, and factory layout optimization. A lot of studies related to simulation techniques have already been conducted in this research area. In many studies, the work time is determined by dividing a total workload by its work efficiency observed on the shop floor. On the other hand, shipbuilding work consists of more supplemental work to main work as workers operate under the constraints of three-dimensional space. Therefore, the conventional method, which consider only main works, cannot adequately respond to the present situation of shipbuilding. To solve this problem, this paper proposes a modeling method for shipbuilding tasks that can represent supplemental works as well. The shipbuilding task is represented as a combination of elemental tasks, and each elemental task is an executable function that can consider a path in three-dimensional space. Based on this model, a multi-agent simulator for shipbuilding is developed. The simulator considers a virtual shipbuilding factory as an environment and workers as agents. By comparing the results of the simulation in a sub-assembly process with the actual work in a shipyard, it was found that the simulator can properly approximate the time of each task including supplemental works. In addition, this paper discussed the digital transformation of shipbuilding that utilizes this simulator for production planning and production control.
Development of PLM system for precise production planning and production control in shipbuilding
K Matsuo, National Maritime Research Institute
Data integration has become an important issue to respond to shortening delivery time and complex product development in shipbuilding. This paper introduces a development of a prototype system for PLM systems in shipbuilding. The PLM system is developed for the purpose of precise production planning and the production management in the shop floor. Especially, the PLM system is considered as a use case to provide input data which is necessary for production simulators that reproduce precise work procedures at the shop floor .
The data structure in the PLM system is reviewed to provide the necessary data to the production simulator in the beginning of this paper. The data is represented as BOM and BOP (Bill of process), which are associated with product information, process information, and facility information, and is implemented in the PLM system. The data flow from the PLM system to the production simulator is introduced, then a series of demonstrations from the PLM system to the execution of the production simulator are presented, followed by a discussion of the effects and the future issues of the proposed data structure and the PLM system.
Interface development between the 3D CAD software and the structural strength assessment software for efficient classification approval
J Kim, Korean Register
As the ship design has been increasing complexity with the need to drive optimization and performance at the same time, the use of various computer-aided software during the ship design process is no longer an option these days. However, most software basically supports their own proprietary file format which can only be used by their own software, and also requires to reiterate modeling the ship design which had already been used in other software. Often these repetitive works become a major hinder to streamline the design process due to the huge cost of time and effort and may have potential risk for human error. In this regard, interfaces to increase productivity between software for data reusability were developed, but the available data was limited in 2D CAD-based. However, as 3D CAD is adopted in the shipyards, it became possible to access and utilize the 3D modeling data containing all information of the ship design. We have developed the interface function that can carry out hull structural strength evaluation for classification approval very quickly and efficiently based on the 3D CAD model. In this paper, we present the interface between 3D CAD software, NAPA Designer, and classification’s structural strength assessment software, SeaTrust-HullScan, that can dramatically improve design productivity.
About Using the Game Engines in Shipbuilding, Software Developer’s Perspective
G Sikic, LINA et al
During the development of the ShipExplorer suit of the programs, every single detail was carefully designed and implemented using low level libraries like OpenGL. The result was very sophisticated, quality program that delivered top performance with wonderful user experience. However, development of new features required theoretical and practical knowledge about many different disciplines starting from linear algebra, knowledge of OpenGL internals, and proficiency in C++ programming language. The additional problem was that the every new hardware target, like mobile phones, or various HMD models had to be addressed particularly, without any code sharing. At the same time, new class of programs started appearing, so called “Game Engine” programs. This class of programs promised maximum results with a minimum effort. Screenshots with spectacular graphics and pre-generated movies were available, showing the output of these programs. Also, “out of the box” support for all major platforms and various hardware was claimed. Taken together, it was enough to rise a question if approach of using low level libraries was a correct approach in the presence of the tools like “Unreal Engine” or “Unity”. In this paper, author’s experience in working and extending Unreal Engine, will be presented. Problems using C++ programing language and internal “Blueprint” visual scripting in Unreal Engine will be analyzed. Scenario of usage as a visualization and annotation tool will be evaluated and compared to the possible alternative approaches.
Simulation Method of Fleet Transition Based on Technology, Economics, and Regulation Scenario for Decarbonization of Shipping
S Wanaka, National Maritime Research Institute
Decarbonization of shipping is one of the biggest problems in maritime industry. International Maritime Organization (IMO) adopted an initial strategy on the GHG reduction from ship, and the industry has started to consider how to response to the strategy. However, it has progressed rather slowly because of various future uncertainties and interests of stakeholders in the sector. In order to strategically advance the decarbonization, it is necessary to develop tools to discuss how to implement the IMO’s strategy quantitatively.
This paper proposes a method to simulate fleet transition toward the decarbonization based on multiple scenarios of technology, economics, and regulation. The simulation model includes not only technical models such as energy consumption from ship and the GHG emission but also social models of regulation for operation related to CII and operator’s decision-making of which type of fuel to select in each time step. By inputting future assumptions of ship’s performance, fuel prices, regulation, and transportation demand, the simulation projects a transition of fleet, and calculates OPEX, CAPEX, and amount of GHG emission during the transition. The simulation enables the stakeholders of decarbonization of shipping to analyze and compare future possible strategies of the fleet transition quantitatively.
This paper focus on bulk carriers in international shipping. By using the simulation, several cases are calculated based on assumptions of some types of decarbonized ships. The case study demonstrates that the simulation can evaluate the several concepts quantitatively, and it is useful for supporting the stakeholder’s decision-making.
Study on Simulation Based Evaluation of Route and Cargo Specific Project for Introducing Decarbonized Ships
S Wanaka, National Maritime Research Institute
In recent years, International Maritime Organization (IMO) adopted an initial strategy on the GHG reduction from ship. Cargo owners, shipping companies, and ship owners have started to consider how to response to the strategy. Introduction of decarbonized ships is future direction to fulfill the IMO’s strategy. However, for each route and cargo, the situation is different, and it is necessary to consider the introduction plan of decarbonized ships that is appropriate for each.
This paper proposes an evaluation method of introduction project of decarbonized ships. The method assumes specific route and cargo, and scenarios of decarbonization technology, environmental regulation, fuel prices, and infrastructure deployment for alternative fuels, and evaluates costs such as OPEX, CAPEX, and amount of GHG emission based on a simulation of fleet transition. The method provides quantitative evaluation of the introduction project to the stakeholders and supports their decision-making. By changing the inputted parameters, sensitivity analysis to consider future uncertainty can be conducted based on the method.
As a case study, we assume several types of alternative fueled ships, alternative fuel ready ships, and energy saving technology such as wind assist, and evaluate environmental performance and costs of introducing them to iron ore transportation between Australia and the Far East. Scenarios of infrastructure deployment for alternative fuels is assumed as well, and by comparison of the cases, the usefulness of the fuels and technologies in each case is discussed.
About Creating Open-source 3D Modular Viewer in Python
G Sikic, LINA et al.
During the development of the ShipExplorer suit of the programs, a great attention was given to the process of building the application, modularization and code organization. During that period, a successful cooperation with FAMENA was established, resulting in a new requirements that students with no real experience in SW development create new modules that will solve some specific problems. After the ShipExplorer project was put on hold, it was decided to start a new project with a similar objectives, that will fulfill FAMENA requirements from the start, and also help save and use huge knowledge base gained during development of ShipExplorer. As a result project “3D Modular Viewer” was created. In this paper, experience designing and implementing 3DM viewer will be presented, as well as problems that had to be solved. The chssoice of programming language will be discussed, together with an additional constraints resulting from that decision. Design decisions and implementation details will be reviewed and the results will be compared with original program, ShipExplorer.
Development of a communication platform to support consensus-building among stakeholders in shipping decarbonization
K Takahashi, Mitsubishi Research Institute, Inc.
In recent years, decarbonization has become an issue in international shipping to solve climate change. In order to find a concept of environmentally friendly vessels, design conditions such as engine fuel technology development, fuel supply infrastructure development, and regulations, should be taken into account. It seems not realistic to achieve zero emissions in a short time without a ship transition over several generations, so that we must bear in mind a variety of scenarios to find a solution. In addition, it is expected that a close coordination is essential for consensus-building of the solution because many stakeholders such as shipbuilding company, shipping company, and shipper have to agree with the solution despite conflicts of different interests between them.
This study defines a process of consensus-building among stakeholders in shipping decarbonization and proposes a communication platform to support it. The designed user interface of the communication platform allows stakeholders to show their requirements and discuss each other based on simulation results, and facilitator to organize and make a consensus. By storing processes of consensus building, the platform may lead a consensus-building process efficiently.
In this paper, firstly, the basic design of a communication system is proposed including the relationships between stakeholders, the requirements of each stakeholder, and the process of consensus-building. Secondly, the basic design of a developed prototype system is described, and results of a case study using the prototype are shown.
Dynamic modelling of ammonia crackers and hydrogen PEM fuel cells for shipping applications
C McKinlay, University of Southampton
The pathway towards the future for more sustainable marine propulsion is unclear. One concept to deliver zero-carbon propulsion that has gained traction in recent years is the use of ammonia as a fuel. This study has focused on using an ammonia cracker (a device to convert ammonia to hydrogen) and a Proton Exchange Membrane (PEM) fuel cell. This process also requires a hydrogen buffer tank and purification. For this study, each of these processes have been dynamically modelled. Simulations show the outputs required to meet the power demand for different vessel types (cargo and survey) for several routes. This has enabled the analysis of ammonia demand and system requirements during several aspects of each route: in port; manoeuvring; cruising; surveying. The same simulations have been run for models of other potential setups to facilitate a fair comparison of the technical challenges, storage requirements, support system requirements (e.g. batteries) and emissions for each concept. Other setups considered included: hydrogen as the main fuel with PEM fuel cells; direct ammonia fuel cells; ammonia combustion.
Japanese Shipbuilding DX Acceleration Through the Application of Public Sector Transformation Strategies
S Crook, SSI
Japanese shipbuilding has long been recognized for the production and on-time delivery of high-quality, innovative ships. Japanese shipyards will continue to remain competitive in an ideal future because of these factors. However, shipbuilding in Japan faces several internal and external challenges that put this future at risk: a generation of highly skilled experts retiring from the workforce, a reliance on institutional knowledge, more competition from abroad, and a demand for new innovative ship types. In addition, Japanese shipbuilders have not evolved their businesses to take advantage of the process enhancements digital technologies support, further adding to the risk of falling behind.
This paper defines DX in the context of shipbuilding and examines how Japanese shipbuilders can accelerate DX within their organizations to stay globally competitive for the long term and overcome industry-wide risks. By highlighting transformation case studies from the Japanese public sector during covid-19 and contrasting the varied DX approaches of Japanese shipbuilders, this paper will provide a DX framework that will help the Japanese shipbuilding industry avoid the digital cliff.
Performance optimisation of solid oxide fuel cells through wasted heat recovery systems for marine applications
P Manias, University of Southampton
With the ever-increasing demand for emission reductions within the maritime industry, a joint effort is being made to decrease the carbon footprint on board vessels across the globe. One of the ways this may be achieved, is through the introduction of fuel cells as an integral component of a vessel’s powertrain. Specifically, this project examines the application of solid oxide fuel cells in the marine environment, as a means of providing the baseload power for a modern 6000-passenger cruise vessel, to cover the total energy demand on board whilst in port and the ‘hotel load’ during voyages.
This paper investigates effective ways of utilizing any sources of energy that would otherwise be wasted, with the concept of increasing the powertrain system’s overall efficiency and subsequently decreasing its carbon footprint. In this case the feasibility of using heat, dissipated from the fuel cell stacks’ exhaust gasses, to produce steam to meet various demands that occur on a large cruise ship. The estimation of exhaust heat dissipation was achieved using dynamic modelling techniques to simulate the operation of 10.5 MW Solid Oxide Fuel Cells, as a way of assessing their steam producing capabilities.
Finally, an evaluation is completed, into the difference it would make to annual fuel consumption and net exhaust emission reductions of powering these solid oxide fuel cells, with LNG reforming methods or running them directly on pure hydrogen. The fuel cell installation is also compared to a typical LNG fueled engine generator powertrain.
Wind assisted propulsion: Investigations on the use of ship holistic models for performance analysis
A Bellot, LMG MARIN France
Wind propulsion is one of the most promising technologies to reduce carbon intensity of ships. However, with variable thrust production and induced drift action, sail’s contribution to propulsion is to be evaluated in different ways from traditional propulsors. For sail retrofit projects, where vessels are initially designed to be optimal at single transit speeds with propulsion engine, wind assistance may also induce a degradation of operational efficiency and limit the extend of energy savings. For these reasons, performance analysis should evolve to account for complex energy transfers between propulsion domain and energy systems. A novel Modelica based model is presented in this article, where manoeuvres and energy modelling are used jointly to predict overall efficiency of wind assisted ship concepts. The model is used to evaluate the impact of retrofitting 4 Flettner rotors on the Duisburg test case (DTC) equipped with diesel engines mechanical propulsion system, with oil fired and exhaust gases steam plants and electricity generation from gensets and turbo-generator. Finally, from the analysis of DTC performance in a sweep of wind conditions, potential solutions to increase sailing efficiency are presented, offering new research directions in vessel design adaptation to natural propulsion.
From Point Cloud to CAD-model based on AI
J Luetzenberger, Prostep
Most vessels undergo modernization and overhaul during their lifecycle. A model representing the as-is status is a pre-requite to plan these activities. Especially when it comes to overhauling a piping system, it is crucial to know their exact spatial layout. Otherwise, the existing parts and the newly delivered parts may not fit together.
Capturing the surfaces of the parts using a 3D scanner and generating a point cloud representing the as-is situation is state of the art. The point cloud is then loaded into a CAD system to represent the existing parts before designing the new parts and ensure they fit together seamlessly. This necessitates remodelling at least the connection points of the existing parts manually. Remodelling is both time-consuming as well as error-prone, so we’d like to avoid it.
In the DigiTwin research project, we developed a solution for this. It features a fully automatic generation of a CAD model based on recognizing piping components from the point cloud using artificial intelligence. The main task is running object recognition from the point cloud. It is crucial to find the correct components and detect their position. Based on that, we generate native CAD models for typical shipbuilding tools. This enables using the automatically generated CAD models for the as-is status as reference geometry for the updated design. In our paper, we’d like to present the steps needed to do so and also the result we achieved.
The benefits of having a best-in-class shipbuilding tool
R Perez Fernandez, Siemens Digital Industries Software
With the acquisition of FORAN by Siemens, it is expected to enhance the marine design and engineering capabilities soon.
This is the perfect marriage, FORAN, the shipbuilding CAD tool with the longest tradition, and Siemens, always at the state of the art of the technology.
This integration will provide a comprehensive portfolio of software and services related to all facets of a ship’s lifecycle, including concept design, production and operations, as well as optimized service lifecycle management.
We have become a key partner for the shipbuilding Industry, and although we are a global leader, we need to retain our customers and gain new ones, and in order to do that, we need to work harder providing them the best solutions.
By creating a best-in-class tool for shipbuilding, leveraging the team’s industry expertise, shipyards and technical offices will be able to have a better control of their ship design and manufacturing process as they transition to Shipyard 4.0.
There is a lot of work out-there, waiting for us to achieve a greater success, big customers with big needs, and Siemens will provide the best solution as possible.
A New Approach For Using Cad And Plm Integration
R Perez Fernandez, Siemens Digital Industries Software
During the last decades, a tight and efficient integration between the CAD and the PLM systems used in complex shipbuilding products, definition, manufacturing and operation has become a more and more important matter, in order to ensure design efficiency, avoid design errors, prevent wasting time in using wrong data or, simply, to provide a common environment in which different organizations and partners working in the same shipbuilding design programs must share their data and follow common procedures.
When we talk about CAD and PLM integration, we must distinguish between CAD systems that use individual files to store the data (files that must be put under a PLM system control to be properly managed) and CAD applications that use their own database as a data repository.
The first one is a classic mechanical CAD to PLM integration approach, while the second is actually a proper case of systems integration, as both applications make use of their own database and both of them have to be maintained linked and synchronized, in order to guarantee data consistency and, as well, to ensure that the principle of the PLM as the “single point of truth” is maintained.
In this paper, we will be centered in the database CAD systems approach, the one used for a complete integration between FORAN and Teamcenter, where there is an increment in productivity and ease of use go together when using these new capabilities.
Semi-Automatic Distributed Ship Service Systems Routing Framework for Submarine Early-Stage Design
M H Mukti, University College London
Part of submarine design complexity is that they are typified by extensive and densely engineered distributed ship service system(s) (DS3). Even though the submarine early stage design is the phase to address major DS3 choices in the design process, in initial sizing and submarine synthesis reliance is often made on “past practice” and simple vessel displacement-based weight algorithms. Such an approach not only inhibits the ability of the concept designer to consider the impact of different DS3 options but also ignores the opportunity (or necessity) to undertake Requirements Elucidation, more specifically for DS3. One of the greatest challenges of DS3 synthesis is the development of the routing model of cables, ducts, and piping which can be time-consuming to be done in Early Stage Ship Design (ESSD). Thus, this paper proposes a novel method for early stage routing of DS3 for a submarine. The approach uses network descriptions of the DS3 topology and computer-aided ship design (CASD) to produce DS3 routing rapidly in ESSD. The usefulness of the approach as an early stage design tool is demonstrated by using it to design the routing for various DS3 of a conventionally powered submarine.
Development of a low-cost real-time ocean wave observing system based on deep learning image algorithm
J Choi, Daewoo Shipbuilding & Marine Engineering Co., LTD.
Obtaining accurate real-time wave information about actual ships sailing at sea was expensive and uncertain. In this study, as a low-cost solution, a real-time ocean wave observation system was developed which provides wave information of the ship in the route the actual ship sailed. The system consists of a camera, motion sensor, GPS, and mini-PC. The ocean image of the system used a deep-learning algorithm model, which has image processing power to observe the wave height, wave direction, and wave period. The training image data of the deep-learning algorithm was collected from two different ships, both of which were equipped with a wave radar system. The deep-learning algorithm model was subjected to various types of verification and testing, and finally we showed excellent prediction results and errors. The ocean wave information observed by this system is linked to the ship digitalization platform system and linked with a dedicated satellite antenna connected to the network, it can check real-time measurement information not only on ships but also on land. This system is expected to be used for the safe operation of ships.
Digital Transformation Through Data-Driven and Data-Centric Approaches with Artificial Intelligence
J Khairuddin, Universiti Teknologi Malaysia
The data-driven approach emphases on extracting information and insights from the input data into executing the next course of action. While the data-centric approach focuses on exploiting the domain specific knowledge using the existing data and their relationships into producing a new near accurate output. Exploring the advantages, they both serve as the key to the ship industry digital transformation which defines the related innovations and the use of digital technologies to deliver the processes, product quality, cost and organisational improvements. Moreover, digital transformation is viewed to have an important role in making the industry remain competitive and relevant in the current era. Consequently, this work reviews the potential, impact and challenges of adopting the data-driven and data-centric approaches in supporting ship design and building processes, engineering analysis, simulation, experimentation and verification. Case studies are explored at the UTM Marine Technology centre (MTC) on the approaches, especially on the design, simulation and analysis tools, intelligent towing tank, AI and IoT technologies applications. They present significant potential and impact on the existing processes and productivities with focus on the data collection, modelling, validation and optimization. Therefore, the findings open a new venture into expanding the use cases, technologies and processes improvements.
AI/ML applications for ship design
M Wheeler and J Hodges, Siemens Industry Software Computational Dynamics Limited
With stricter regulations on emissions, ship designers need to understand a vessel’s powering requirements more accurately than ever. Traditional methods include scaling experimental data to full scale, which relies on estimations. Full scale CFD simulations are also an option, but can take a long time to execute making these types of analyses less practical for daily design decisions. Reduced order and machine learning models can be applied based on a set of designs that can be executed early in the design state. Then, these models can be used to instantly understand powering requirements as the design process marches forward. This work uses Simcenter STAR-CCM+ to generate the CFD data, and Simcenter ROM builder and Monolith AI for using that data in a no-code machine learning platform. Firstly, in terms of capabilities, the machine learning models were able to predict several 0D performance metrics (heave, pitch, total resistance, and propulsion metrics) with respect to 12 independent geometrical parameters involved in the ship design. These predictions were then supplemented with additional machine learning predictions of the spatial field as well, in order to provide designers with more information. Regarding the spatial fields, there are two main capabilities the machine learning models provided: predict results of spatial fields in the form of local contours (on the hull, free surface, and in flow into the propeller), and thereby also an optimization pipeline which can morph the geometry according to the desired cost function for any combination of these machine learning predictions.
Sponsors
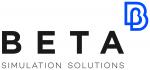
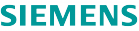


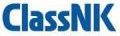
